Amateur Rocket Construction
This website will serve as a comprehensive guide to designing and testing your amateur rocket. As part of my IB CAS Project, I will be sharing my personal experiences and insights throughout the process. Whether you're a seasoned rocket enthusiast or a complete beginner, this website will provide you with the information and resources you need to get started.
Design and Testing Overview: Designing and testing a rocket is a meticulous process that requires attention to detail and a solid understanding of basic principles. This website aims to break down the complexity into manageable steps, making it accessible for everyone. We'll cover the fundamental aspects of rocket design, including aerodynamics, propulsion, and stability, and provide practical tips and tricks for each stage of the process. By following along, you'll not only learn how to design a rocket but also gain insights into the iterative nature of engineering, where testing and refining are crucial to success.
Personal Insights and Experiences: Throughout this journey, I will share my personal experiences, including the challenges I faced and the solutions I found. This project has been an incredible learning experience for me, and I hope to pass on valuable lessons that can help you avoid common pitfalls. From initial design concepts to the final launch, every step has its unique set of hurdles, and understanding these can make your own rocketry endeavors smoother. By documenting my process, I aim to create a resource that not only educates but also inspires you to pursue your own projects with confidence and curiosity.
Resources and Community Engagement: In addition to technical guidance, this website will provide a wealth of resources, including links to useful tools, software, and community forums where you can connect with fellow enthusiasts. Engaging with the rocketry community can provide additional support and motivation, as well as opportunities to collaborate and share knowledge. Whether you're looking for troubleshooting advice, inspiration for new designs, or simply a place to share your successes, these resources will be invaluable in your journey.
Introduction to Rocketry (!!! SAFETY !!!)
Before we dive into the technical aspects of rocketry, it's important to discuss safety. Rocketry can be a dangerous activity, so it's essential to understand the risks involved and take the necessary precautions. This section will cover basic safety protocols, such as wearing protective gear and launching in a safe location. Additionally, we will discuss the importance of following all relevant laws and regulations.
Disclaimer about Rockets:
It's important to note that rockets are powerful machines and should be treated with respect. This website is intended for educational purposes only and should not be used as a substitute for professional advice. Always consult with a qualified expert before attempting to build or launch a rocket.
Respecting Rocketry's Power: Rockets, by their very nature, are complex and powerful machines that require careful handling and respect. This section emphasizes the importance of understanding the potential dangers and respecting the forces at play. Acknowledging the inherent risks associated with rocketry encourages a cautious and informed approach, reducing the likelihood of accidents and ensuring a safer experience for all involved.
Educational Purpose and Limitations: While this website aims to provide comprehensive educational content, it is not a replacement for professional guidance. Amateur rocketry enthusiasts should always seek advice from qualified experts, particularly when dealing with advanced or potentially hazardous aspects of rocket construction and launching. This section will underline the importance of professional consultation and continuous learning to enhance your understanding and practice of rocketry safely.
Promoting Responsible Practices: Promoting a culture of safety and responsibility is a core value of this website. By providing clear disclaimers and encouraging users to seek expert advice, we aim to foster a community that prioritizes safety and informed decision-making. This section will discuss the broader implications of responsible rocketry practice, including its impact on public perception and the legal landscape, reinforcing the necessity of a cautious and educated approach.
Laws and Regulations:
Rocketry is subject to a variety of laws and regulations, which vary depending on your location. It's important to research and comply with all applicable laws before building or launching a rocket. This section will provide an overview of some of the most common laws and regulations, but it's essential to consult with local authorities for specific requirements.
Understanding Legal Frameworks: Navigating the legal landscape of rocketry involves understanding a complex web of regulations that govern the construction, storage, and launching of rockets. This section will provide an overview of these legal frameworks, highlighting key areas such as airspace restrictions, safety zones, and environmental considerations. By offering a general guide, we aim to equip you with the knowledge to start your research and ensure compliance with all necessary legal requirements.
Research and Local Consultation: Laws and regulations can vary significantly by region, making local research and consultation essential. This section will discuss practical steps for identifying and understanding the specific requirements in your area. We'll cover resources for finding local laws, contacting regulatory bodies, and obtaining necessary permits. By emphasizing the importance of local compliance, we aim to help you avoid legal issues and ensure a smooth and safe rocketry experience.
Adapting to Changing Regulations: The regulatory landscape for rocketry is dynamic and can change in response to technological advancements and safety concerns. Staying informed about these changes is crucial for ongoing compliance and safety. This section will provide tips for keeping up-to-date with regulatory changes, including subscribing to relevant newsletters, joining rocketry organizations, and participating in forums and discussions. By staying informed and adaptable, you can continue to practice rocketry responsibly and legally.
Basic Safety Protocols:
Safety should always be your top priority when working with rockets. This section will cover essential safety protocols such as wearing protective gear, launching in a safe location, and following proper handling procedures. By following these guidelines, you can help to minimize the risk of accidents and injuries.
Protective Gear and Equipment: The use of appropriate protective gear is fundamental to safe rocketry practice. This section will detail the types of protective gear necessary for different stages of rocket construction and launching. From gloves and goggles to specialized clothing, understanding and utilizing the right equipment can significantly reduce the risk of injury. We'll also cover the maintenance and proper use of these safety items to ensure they provide optimal protection.
Safe Launch Practices: Choosing and preparing a safe launch location is critical to minimizing risks. This section will discuss the criteria for selecting a launch site, including distance from populated areas, clearance from obstacles, and consideration of weather conditions. Proper site preparation, such as securing a clear launch pad and establishing a safety perimeter, is equally important. By adhering to these guidelines, you can create a safe environment for both the launch and spectators.
Handling and Storage Procedures: Proper handling and storage of rocket components, particularly fuel and motors, are crucial to safety. This section will provide comprehensive guidelines on safe handling practices, including transporting and storing materials to prevent accidents. We'll also discuss procedures for dealing with potential hazards, such as leaks or malfunctions, and the importance of having emergency protocols in place. By following these protocols, you can ensure a safer rocketry experience from start to finish.
Rocket Designing (OpenRocket)
OpenRocket is a free, open-source software program used extensively for rocket design. It allows users to create detailed models and simulations, covering essential aspects such as aerodynamics, propulsion, and stability. By using OpenRocket, designers can predict how their rockets will perform under various conditions, making it an invaluable tool for both hobbyists and professionals.
Body/Airframe Design: The body or airframe of a rocket serves as the central structure, holding together all other components. It must withstand various stresses during flight, including aerodynamic forces and mechanical vibrations. The choice of materials for the airframe is crucial; they must be both strong and lightweight. Common materials include aluminum alloys, carbon fiber composites, and high-strength plastics. Each material has its own advantages and trade-offs in terms of cost, ease of fabrication, and performance.
Designing the airframe involves creating a shape that minimizes drag while maintaining structural integrity. Simple cylindrical shapes are often used for their ease of manufacturing and aerodynamic efficiency, but more advanced designs might include tapered sections or other modifications to improve performance. OpenRocket allows designers to experiment with different shapes and materials, providing detailed simulations of how each design will perform under various conditions.
In addition to structural considerations, the airframe design must account for the placement of internal components such as the propulsion system, avionics, and payload. Proper integration of these elements ensures that the rocket remains balanced and stable during flight. OpenRocket's modular design tools make it easy to visualize and adjust the placement of these components within the airframe.
Nosecone Design: The nosecone is a critical component of the rocket as it significantly influences aerodynamic performance. Its primary function is to reduce air resistance (drag) and protect the payload. The shape of the nosecone determines how smoothly air flows over the rocket, which directly affects the rocket's speed and efficiency. Common nosecone shapes include conical, ogive, and parabolic, each with distinct aerodynamic properties.
Designing a nosecone involves balancing aerodynamic efficiency with structural strength. A well-designed nosecone minimizes drag, allowing the rocket to achieve higher altitudes and speeds. OpenRocket's simulation capabilities enable designers to model different nosecone shapes and analyze their effects on the rocket's performance. This iterative process helps identify the optimal design for a given mission profile.
The nosecone must also be securely attached to the airframe and capable of withstanding the forces encountered during flight. This requires careful consideration of materials and construction techniques. Lightweight materials like fiberglass or carbon fiber composites are often used for their strength-to-weight ratio. OpenRocket allows designers to experiment with various materials and attachment methods, ensuring the nosecone meets both aerodynamic and structural requirements.
Fin Design: Fins provide stability to the rocket by controlling its orientation and preventing unwanted rotation. Properly designed fins ensure that the rocket maintains a straight flight path, reducing the risk of tumbling or veering off course. The number, size, shape, and placement of fins all influence the rocket's aerodynamic stability.
OpenRocket provides tools for designing and testing different fin configurations. By adjusting parameters such as fin shape, size, and location, designers can optimize stability without sacrificing performance. Common fin shapes include rectangular, trapezoidal, and elliptical, each offering different trade-offs between stability and drag.
In addition to their aerodynamic role, fins must be structurally robust. They experience significant forces during flight, particularly at high speeds. Material choice and attachment methods are crucial factors in ensuring fins remain securely attached to the airframe. OpenRocket's simulations help designers identify potential issues with fin strength and attachment, allowing for iterative improvements.
Rocket Motor Choices: The rocket motor is the core component that provides the thrust needed for liftoff and sustained flight. Different types of motors, such as solid, liquid, and hybrid, offer varying thrust levels and burn characteristics. Selecting the right motor involves considering factors like the rocket's weight, desired altitude, and specific mission requirements.
OpenRocket includes a comprehensive database of rocket motors, allowing designers to simulate and compare different options. This helps identify the motor that best meets the performance goals of the project. In addition to thrust, other factors such as burn duration, specific impulse, and reliability are considered in the selection process.
The integration of the motor with the rocket's airframe and other components is also crucial. Proper alignment and secure attachment are necessary to ensure that the thrust is directed correctly and that the motor remains attached throughout the flight. OpenRocket's tools facilitate the design and testing of these critical aspects.
Rocket Simulations (OpenRocket)
Simulating rocket flights using OpenRocket allows designers to predict how their rockets will perform before actual construction and launch. These simulations can reveal potential issues and provide valuable data for optimizing designs. By setting up and running detailed simulations, designers can iteratively improve their rockets, ensuring better performance and safety.
Simulation Conditions / Setup: Accurate rocket simulations require careful setup of simulation conditions. This includes defining parameters such as launch angle, wind conditions, and payload weight. Each parameter can significantly impact the simulation results, so it's crucial to set them up correctly. OpenRocket provides a user-friendly interface to input these conditions, allowing for precise control over the simulation environment.
Setting up the simulation environment involves specifying the physical and environmental conditions under which the rocket will be launched. This includes parameters such as launch angle, wind speed, and direction, as well as atmospheric conditions like temperature and pressure. Accurate input of these conditions ensures that the simulation results are realistic and useful for predicting actual performance.
In addition to environmental conditions, the simulation setup includes details about the rocket itself. This involves specifying the dimensions, weight, and configuration of the rocket, as well as the characteristics of the propulsion system. OpenRocket allows for detailed input of these parameters, providing a comprehensive simulation environment.
Simulation Output Interpretation: Interpreting simulation results is a critical step in the design process. Simulation graphs and data provide insights into various aspects of the rocket's performance, such as altitude, velocity, and stability. Understanding these results helps designers make informed decisions about modifications and improvements. OpenRocket offers detailed visualization tools to help users analyze and understand their simulation outputs effectively.
The primary outputs of a rocket simulation include trajectory plots, velocity profiles, and stability analyses. These data points provide a detailed picture of how the rocket will perform under the specified conditions. Designers can use this information to identify potential issues and make necessary adjustments to the design.
In addition to basic performance metrics, simulations can provide insights into more complex phenomena such as aerodynamic forces, structural loads, and thermal effects. Understanding these aspects is crucial for ensuring the rocket's integrity and performance. OpenRocket's advanced simulation tools enable designers to explore these factors in detail.
Digital Prototyping using 3D models
3D printing technology has revolutionized the way prototypes are developed, offering a rapid and cost-effective method for creating physical models of rocket designs. This section will cover the process of exporting designs from OpenRocket, performing fit tests, and creating custom parts using 3D modelling software.
Exporting models from OpenRocket: OpenRocket allows users to export their designs in various file formats compatible with 3D modelling programs. This step is crucial for transitioning from digital design to physical prototype. By exporting the designs, users can import them into 3D modelling software to prepare for printing. This process ensures that the physical model accurately represents the digital design, facilitating effective testing and validation.
The export process involves converting the rocket design into a format that can be read by 3D modelling software. Common formats include STL (stereolithography) and OBJ (object file), which are widely used in the 3D printing community. OpenRocket provides tools for exporting designs in these formats, making it easy to transition from digital to physical prototypes.
3D Environnement Fit Tests: Before committing to a full-scale 3D print, it is essential to perform fit tests within the 3D modelling environment. These tests help ensure that all parts of the rocket fit together correctly and function as intended. Identifying potential issues at this stage can save time and resources by allowing for adjustments before the physical printing process begins. Fit tests also help verify the accuracy of the exported model and the feasibility of the overall design.
Fit tests involve assembling the digital model of the rocket in the 3D modelling software to check for any alignment or interference issues. This process helps identify areas where adjustments are needed, ensuring that the final printed parts will fit together seamlessly. By addressing these issues in the digital environment, designers can avoid costly mistakes in the physical prototyping stage.
Fiddling with File Formats: 3D printers can use a variety of file formats. This section will discuss the different file formats and how to convert your files if necessary. Understanding the differences between these formats and their specific requirements is crucial for successful 3D printing. Common formats include STL, OBJ, and AMF (Additive Manufacturing File), each with its advantages and limitations.
Converting between file formats involves using software tools to translate the design from one format to another. This process may require adjustments to ensure that the converted file maintains the accuracy and integrity of the original design. By understanding the nuances of different file formats, designers can ensure that their models are compatible with their 3D printing equipment
Custom Part Modelling: Creating custom parts using 3D modelling software allows for greater flexibility and precision in rocket design. Custom parts may be necessary for unique components or modifications not available in standard libraries. This section will provide an overview of how to use 3D modelling software to design and create custom parts, enhancing the overall capability and performance of the rocket. By leveraging 3D modelling, designers can push the boundaries of their creativity and engineering skills.
Custom part modelling involves using 3D modelling software to create detailed designs of unique components. This process allows designers to tailor parts to their specific needs, ensuring optimal performance and integration with the rest of the rocket. Advanced modelling techniques can be used to create complex shapes and structures, expanding the possibilities for innovative design solutions.
Fit Tests & Separate Unit Testing
Once 3D models are created, performing fit tests and separate unit tests is critical to ensure all parts work together seamlessly and meet strength and durability requirements. These tests are essential steps in validating the design and ensuring the rocket's readiness for assembly and launch.
Small Scale Fit Tests: Conducting small-scale fit tests on key components before full-scale printing is a prudent approach. These tests help identify potential issues early in the process, allowing for adjustments and refinements. By focusing on critical components, designers can ensure that these parts meet the required specifications and function correctly within the overall assembly. Small-scale fit tests are a cost-effective way to validate design choices and improve the reliability of the final product.
Small-scale fit tests involve printing and assembling individual components or subassemblies of the rocket. This process allows designers to check for proper fit and function without committing to a full-scale print. By identifying and addressing issues at this stage, designers can refine their designs and ensure that the final product will perform as expected.
Gradual Part Validation: As each part of the rocket is 3D printed, it is essential to validate it against the design specifications. This involves checking dimensions, fit, and functionality. Gradual validation helps identify discrepancies and make necessary corrections before proceeding with subsequent parts. This iterative process ensures that each component meets the required standards and contributes to the overall success of the project.
Independent Unit Tests: Testing separate units for functionality ensures that each part of the rocket works as intended. This includes testing propulsion systems, avionics, and other critical components. Functional testing helps verify that these units perform correctly under expected conditions, providing confidence in the overall design. By testing each unit separately, designers can isolate and address any issues, ensuring that the final rocket operates reliably.
Separate unit functional testing involves setting up and operating individual components or subsystems of the rocket. This process allows designers to verify that each unit functions correctly and meets performance requirements. By testing components individually, designers can identify and resolve issues before integrating them into the complete rocket.
Flight System Integration
Once you have all of the parts for your rocket, you can start to integrate them into a complete flight system. This section will discuss the different components of a flight system and how to integrate them.
Flight Computer Designs:
A flight computer is a vital component of a rocket, responsible for controlling various functions and collecting data during flight. Designing an effective flight computer involves selecting the right hardware and software, integrating sensors, and ensuring reliable operation under extreme conditions.
Hardware Selection: Choosing the right hardware for the flight computer is crucial for its performance and reliability. This involves selecting processors, memory, and interfaces that can handle the rocket's data processing needs. Robust and lightweight hardware is preferred to withstand the stresses of flight. Detailed planning and research are essential to ensure that the selected components meet the specific requirements of the rocket project.
Software Development: The software for the flight computer must be meticulously developed to control the rocket's functions accurately. This includes programming for data acquisition, control algorithms, and communication protocols. The software must be tested extensively to ensure it performs reliably under all expected conditions. Developing custom software allows for greater flexibility and optimization, ensuring the flight computer meets the unique demands of the rocket.
Integration with Sensors: Integrating sensors with the flight computer is essential for collecting accurate data during flight. Sensors may include accelerometers, gyroscopes, pressure sensors, and GPS modules. Ensuring that the flight computer can process and respond to sensor data in real-time is critical for maintaining control and stability. Proper integration involves both hardware connections and software algorithms to interpret and act on the sensor data effectively.
Points of Failure in Integration:
Identifying and addressing potential points of failure during the integration of rocket components is crucial for ensuring a successful flight. This involves a thorough analysis of all systems and interfaces to mitigate risks and enhance reliability.
Common Points of Failure: Common points of failure in rocket integration include mechanical connections, electrical interfaces, and software communication. Mechanical failures may arise from weak joints or improper fit, while electrical failures can result from poor connections or incompatible components. Software failures often occur due to bugs or inadequate handling of edge cases. By identifying these potential issues early, designers can implement measures to prevent them.
Mitigation Strategies: Implementing robust mitigation strategies is essential to address potential points of failure. This involves reinforcing mechanical connections, ensuring reliable electrical interfaces, and thoroughly testing software. Redundancy can be built into critical systems to provide backups in case of failure. Regular inspections and rigorous testing protocols help identify and resolve issues before they impact the rocket's performance.
Testing and Validation: Extensive testing and validation are necessary to ensure that all systems work together seamlessly. This includes conducting integration tests to verify that components function correctly when combined and performing stress tests to simulate real-world conditions. By validating the integrated systems, designers can ensure that the rocket is ready for a successful flight, minimizing the risk of failure.
Full Rocket Dress Static Testing:
Full rocket dress static testing is a comprehensive test of the rocket's systems and components before actual launch. This involves assembling the rocket, conducting a series of tests to ensure everything functions correctly, and addressing any issues that arise.
Assembly and Preparation: The first step in full rocket dress static testing are assembling the rocket with all its components. This includes installing the motor, attaching fins, integrating the flight computer, and ensuring all connections are secure. Detailed checklists and procedures are followed to ensure that the assembly is performed correctly and safely.
Functional Testing: Once assembled, the rocket undergoes a series of functional tests to verify that all systems are working as intended. This includes testing the flight computer, checking sensor outputs, and verifying communication links. Functional testing helps identify any issues with individual components or their integration, allowing for corrections before the final test.
Static Fire Test: The static fire test is a critical component of full rocket dress testing. This involves firing the rocket motor while the rocket is securely held in place. The test simulates the conditions of actual flight, allowing designers to observe the rocket's performance and identify any issues. Data collected during the static fire test is analyzed to ensure that the motor and other systems function correctly under real-world conditions. This test is essential for validating the rocket's readiness for launch and ensuring a successful mission.
Media Gallery
.jpg)
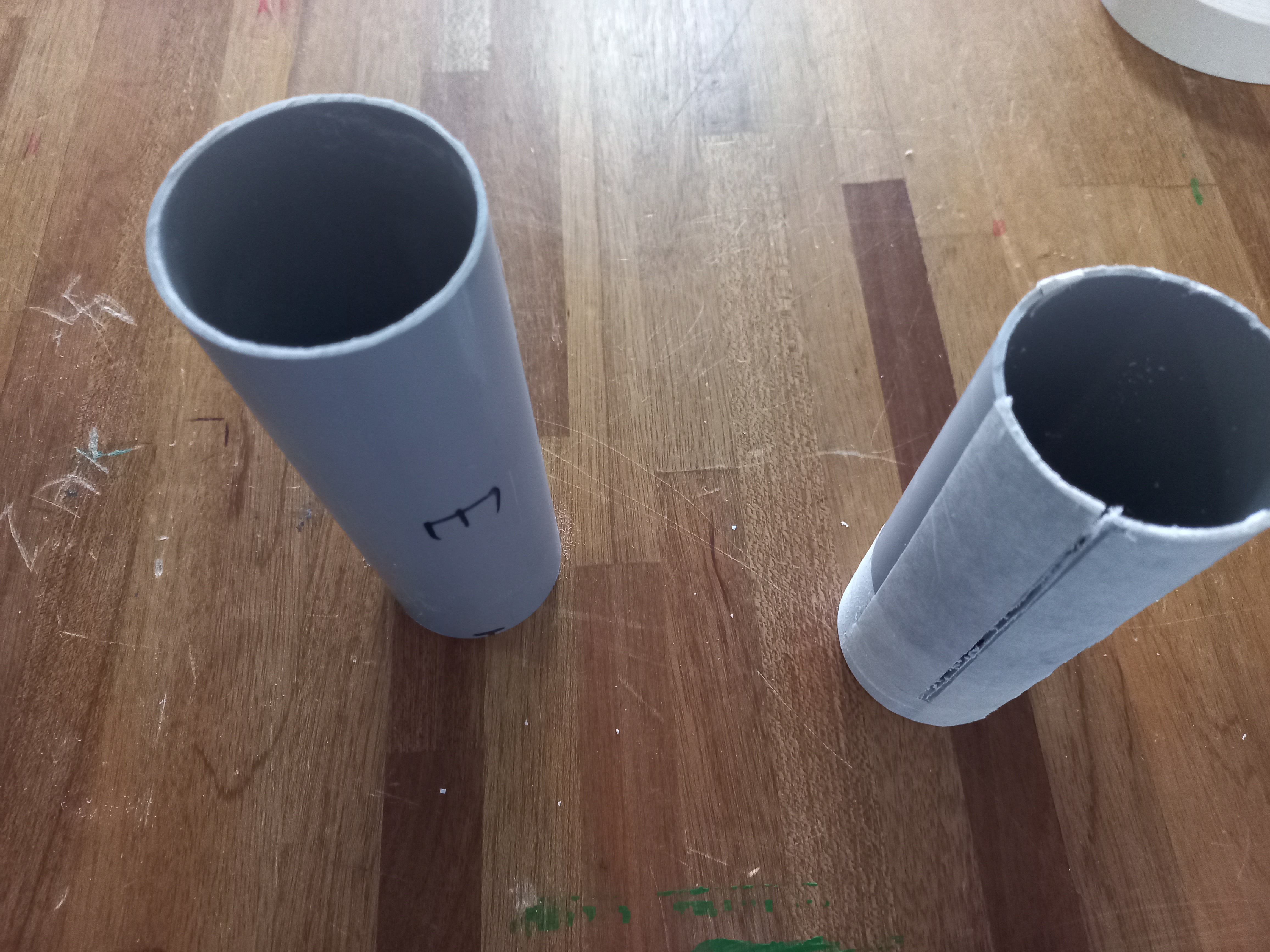
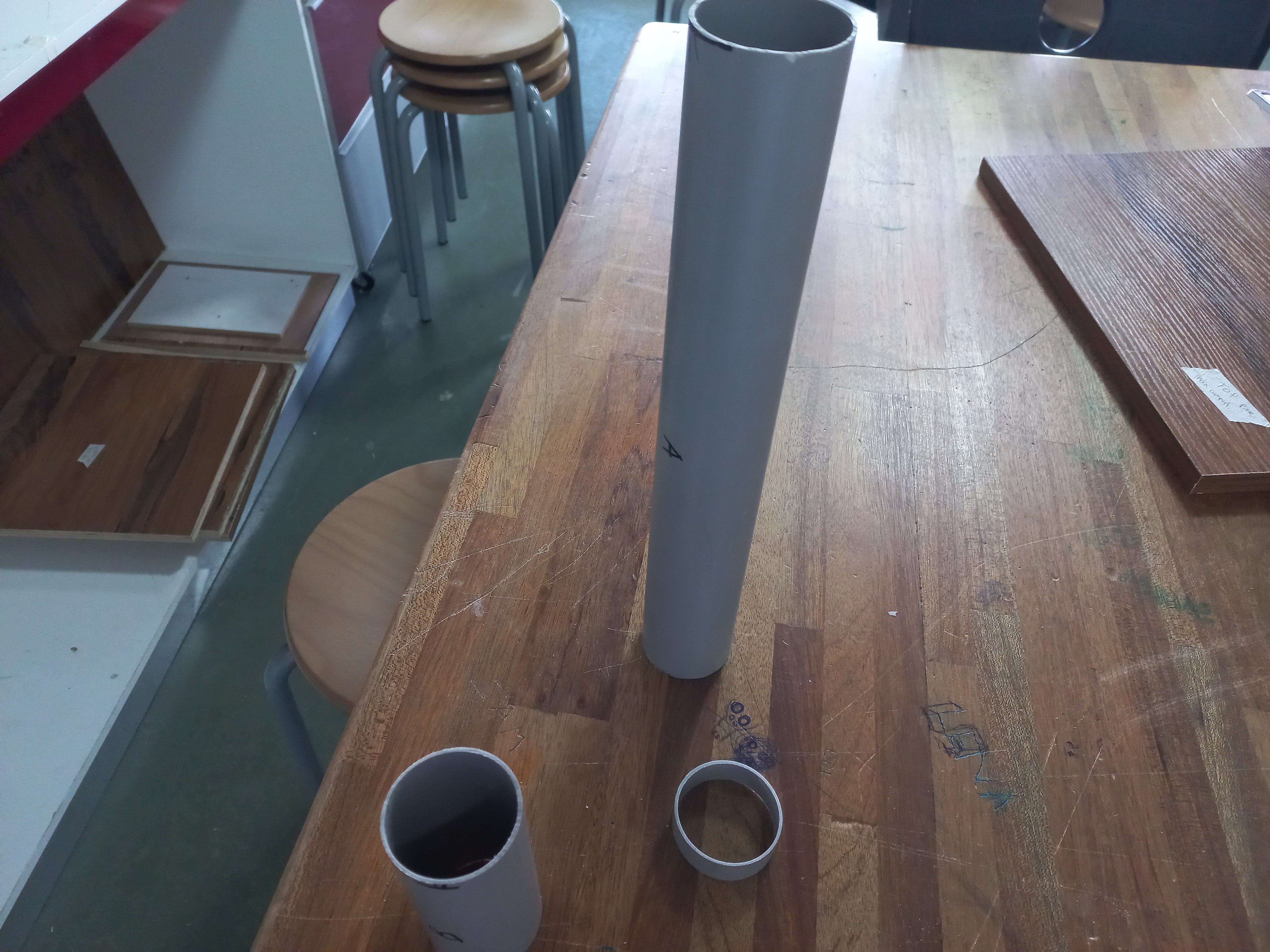
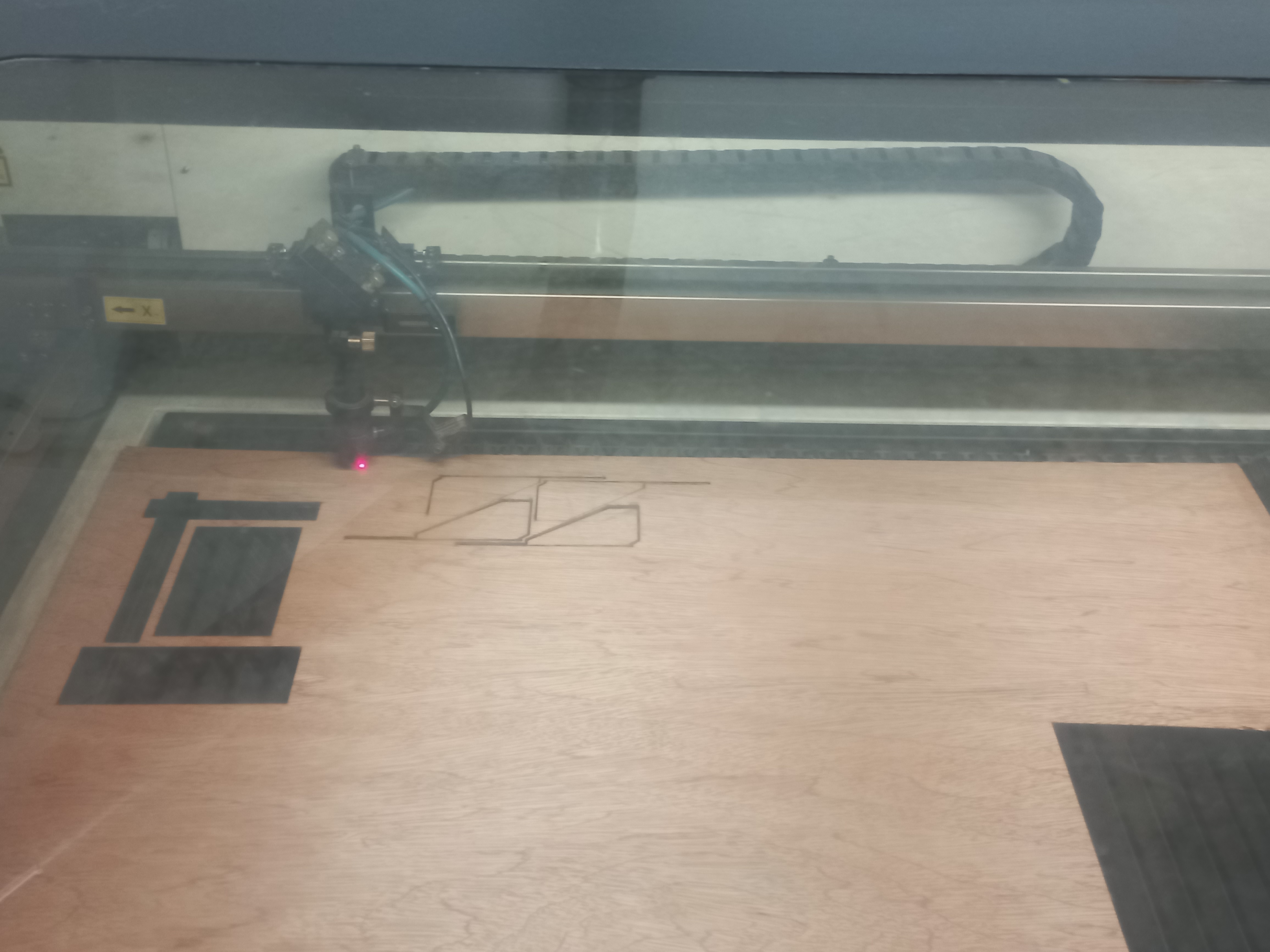
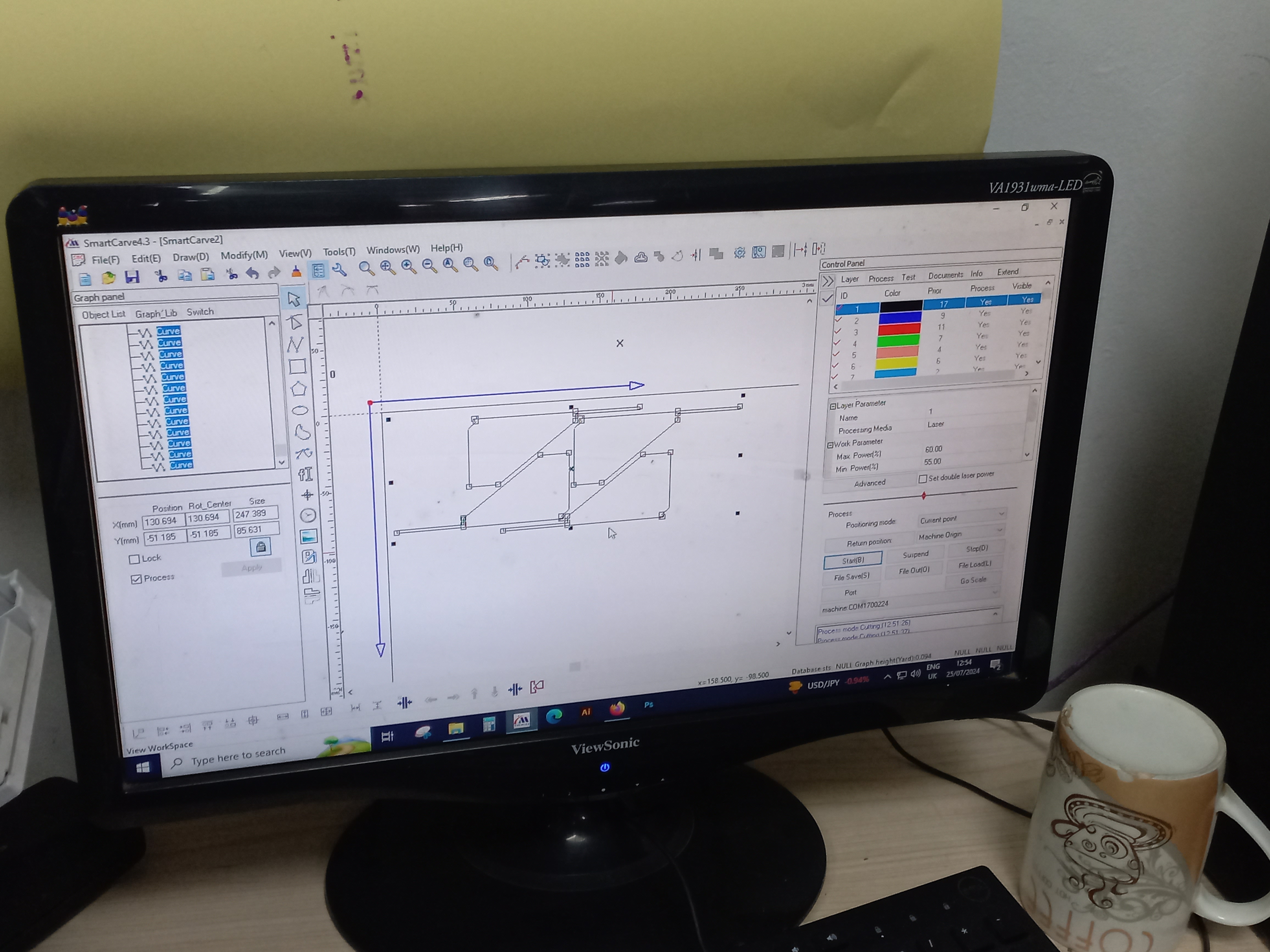
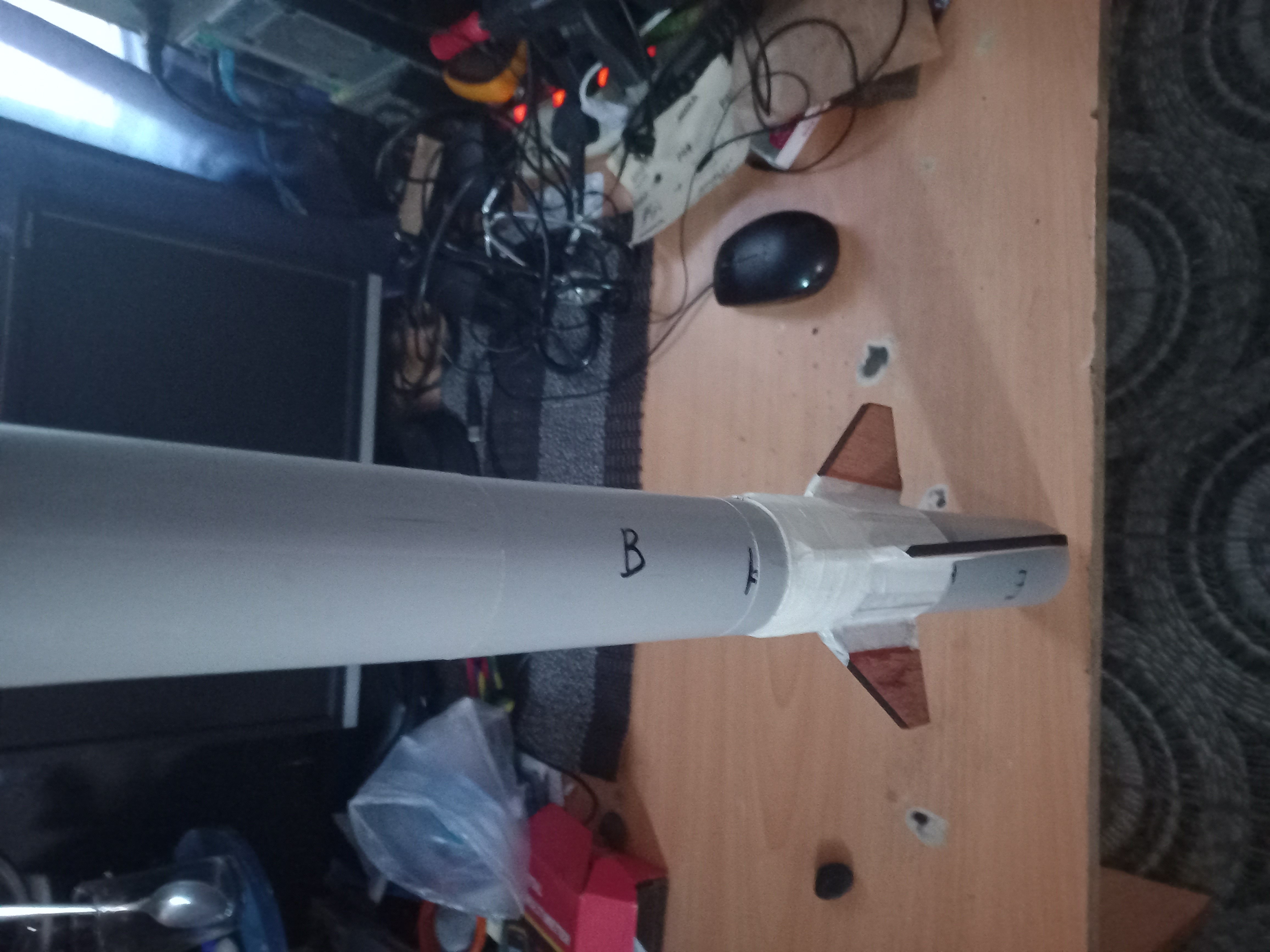
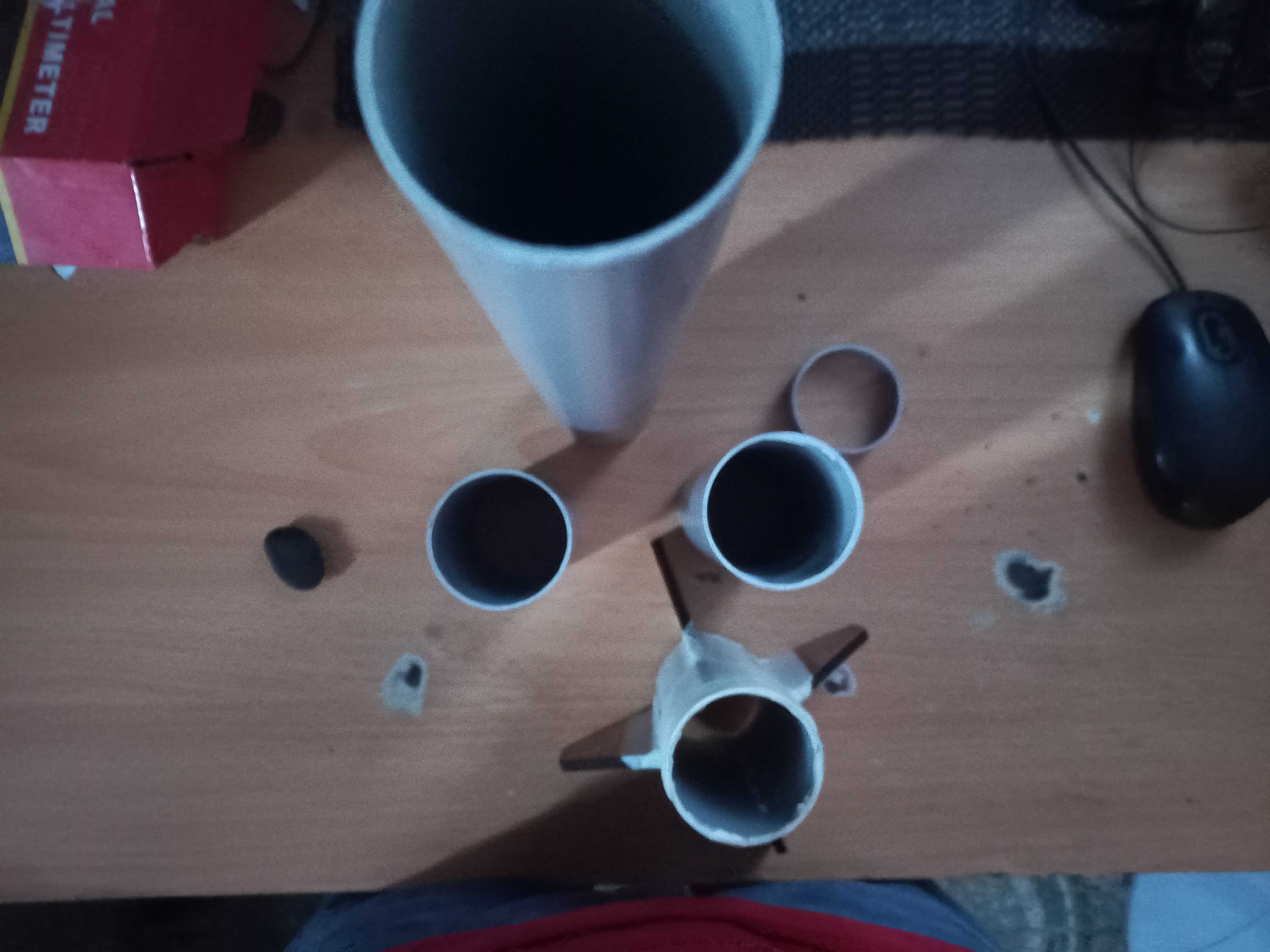
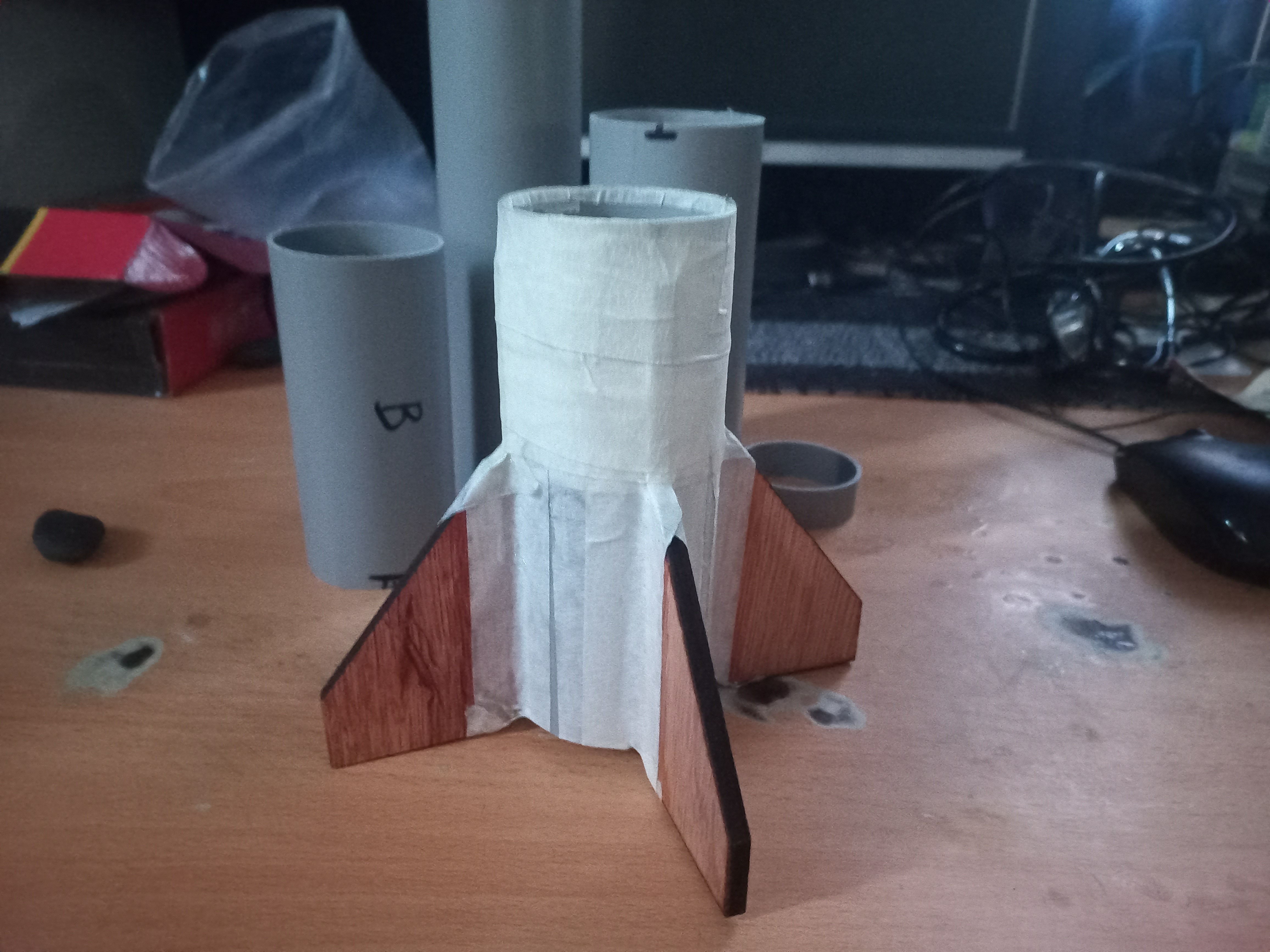
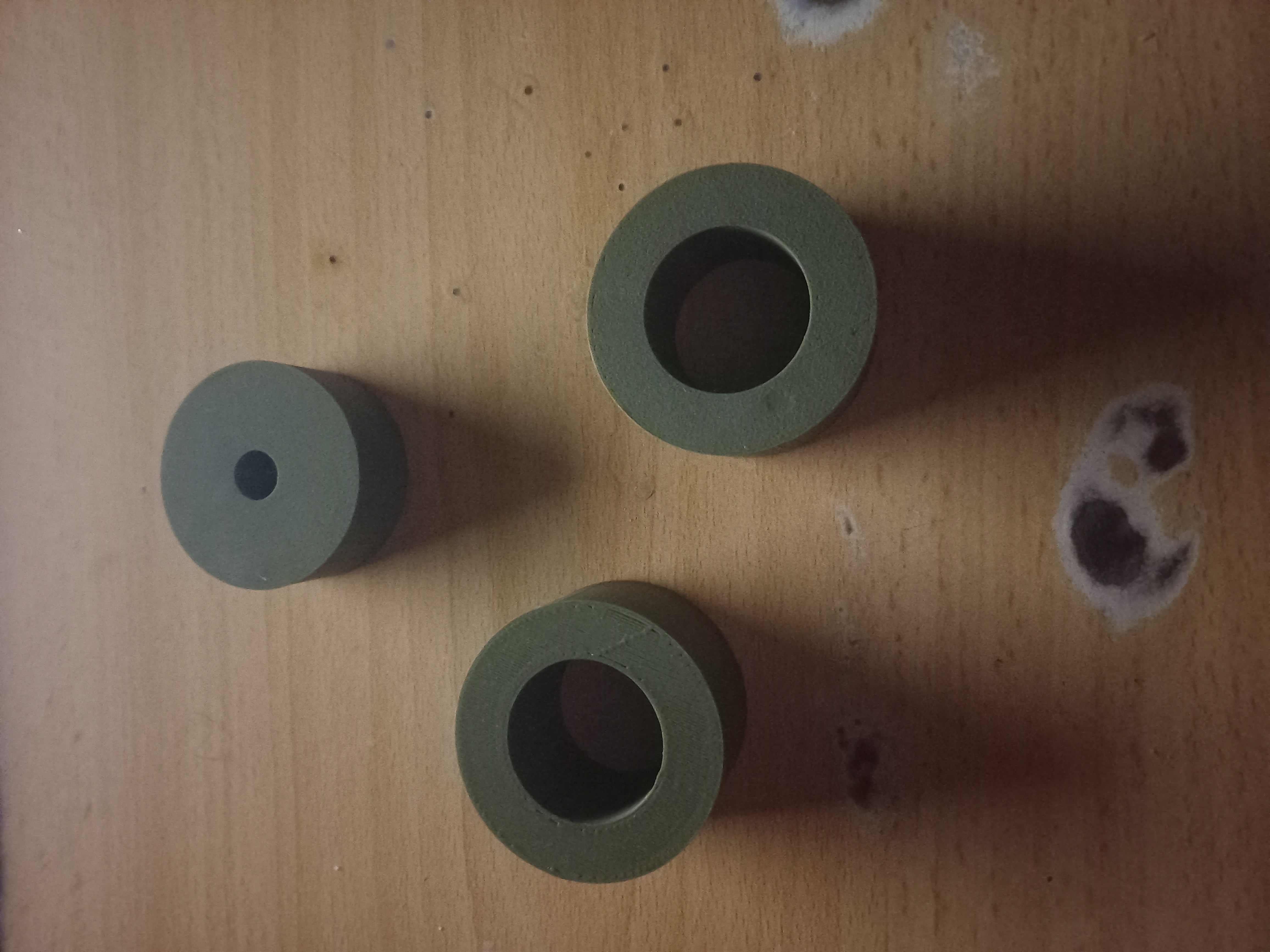
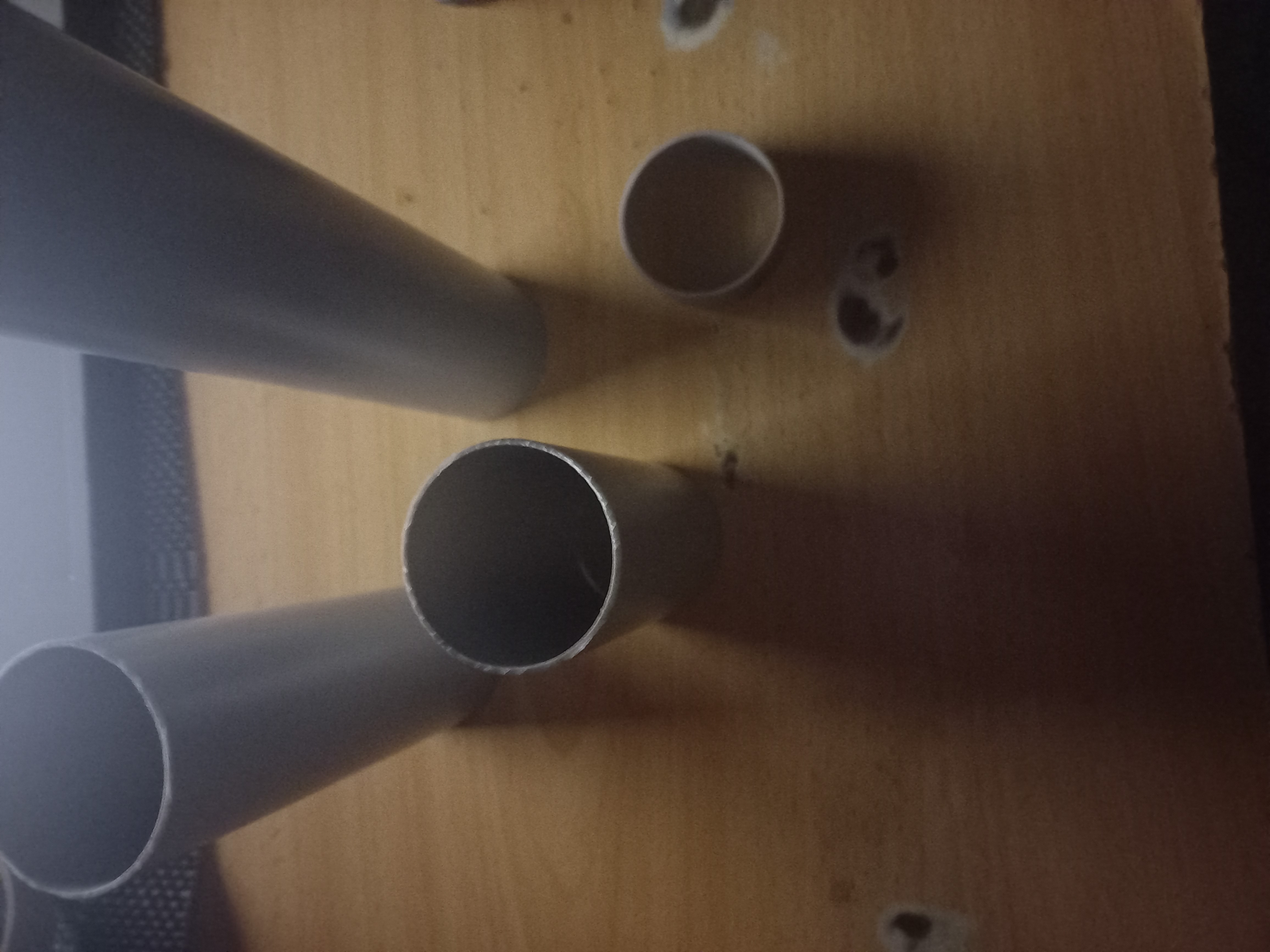
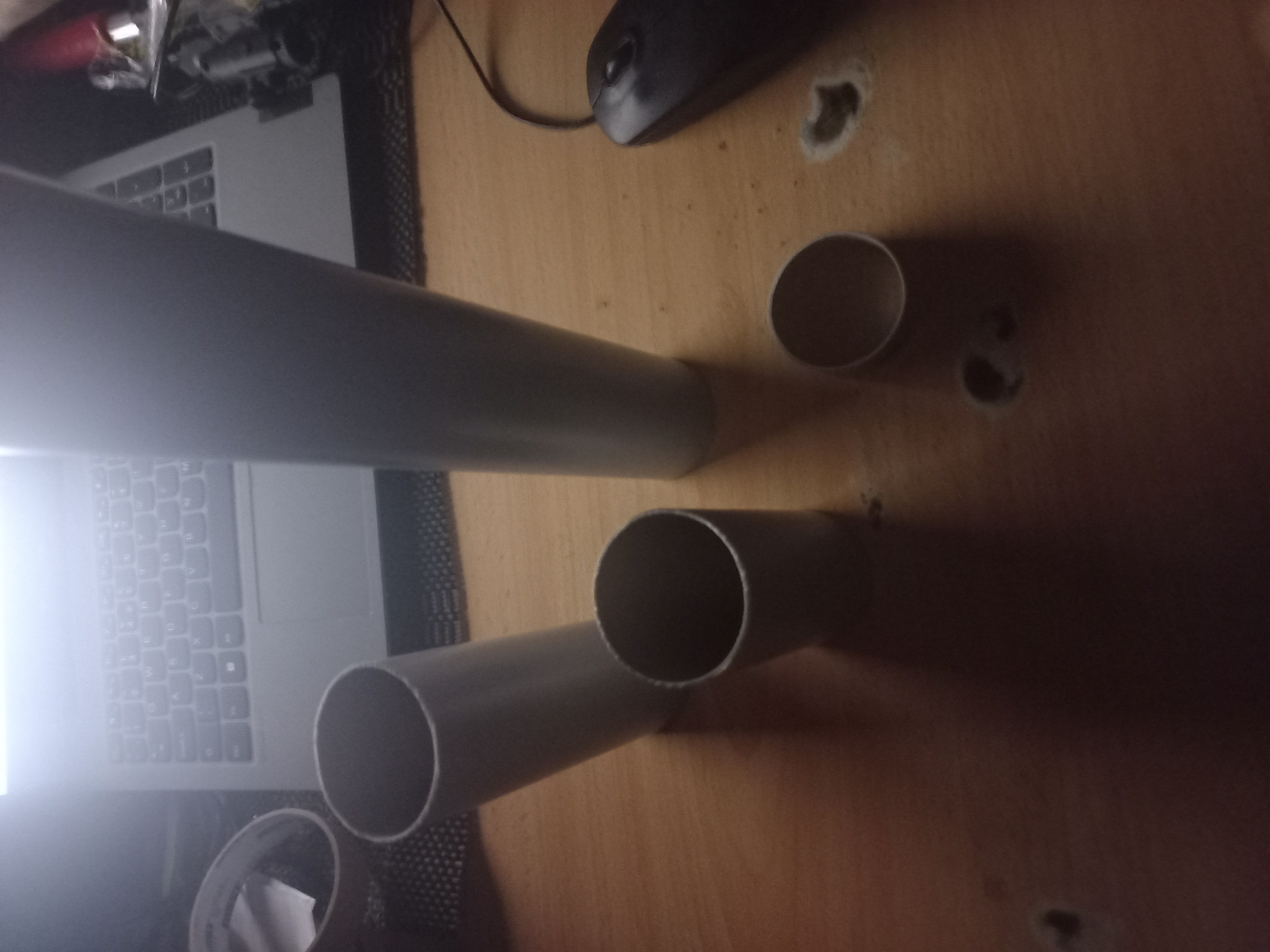
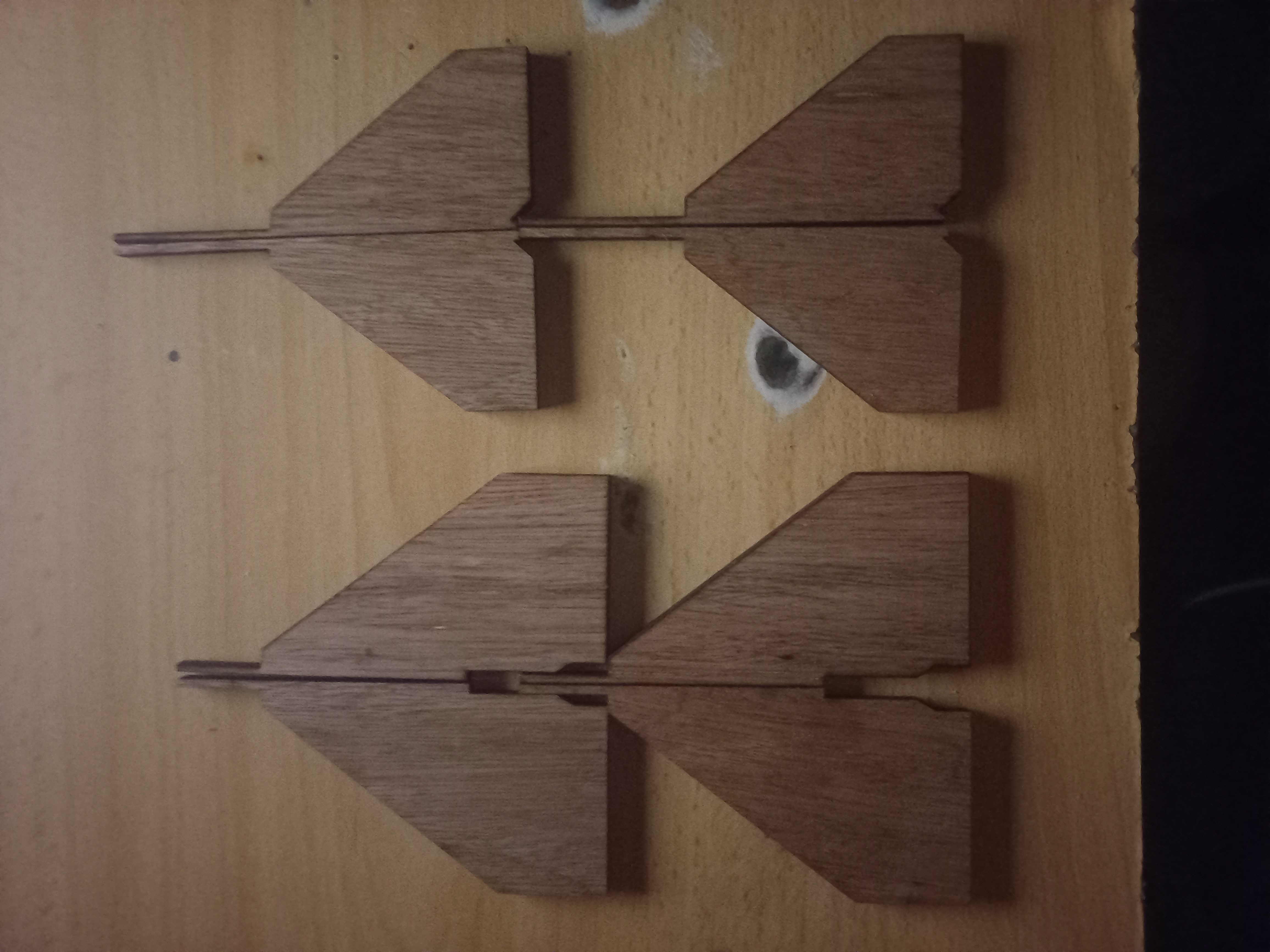
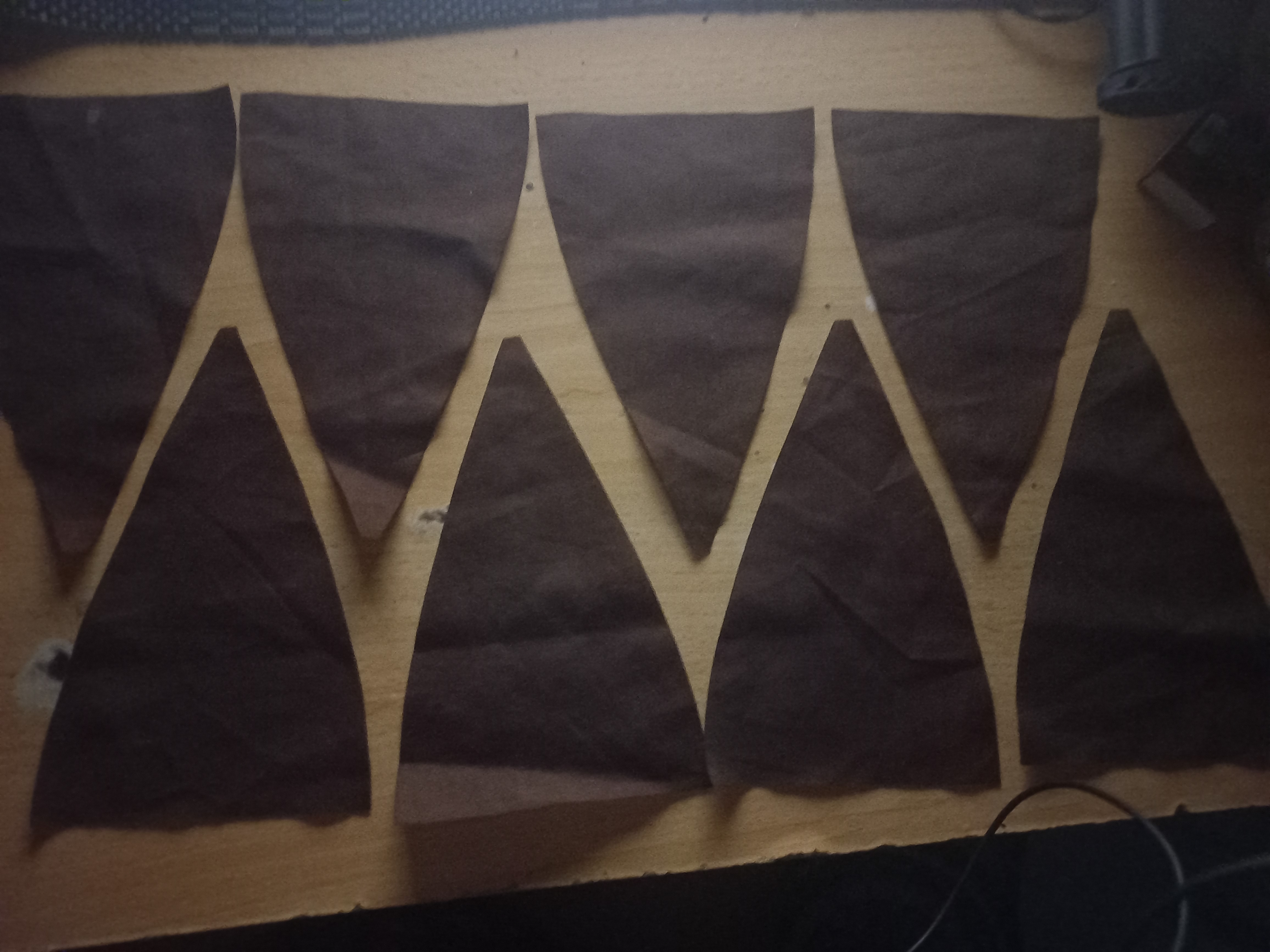
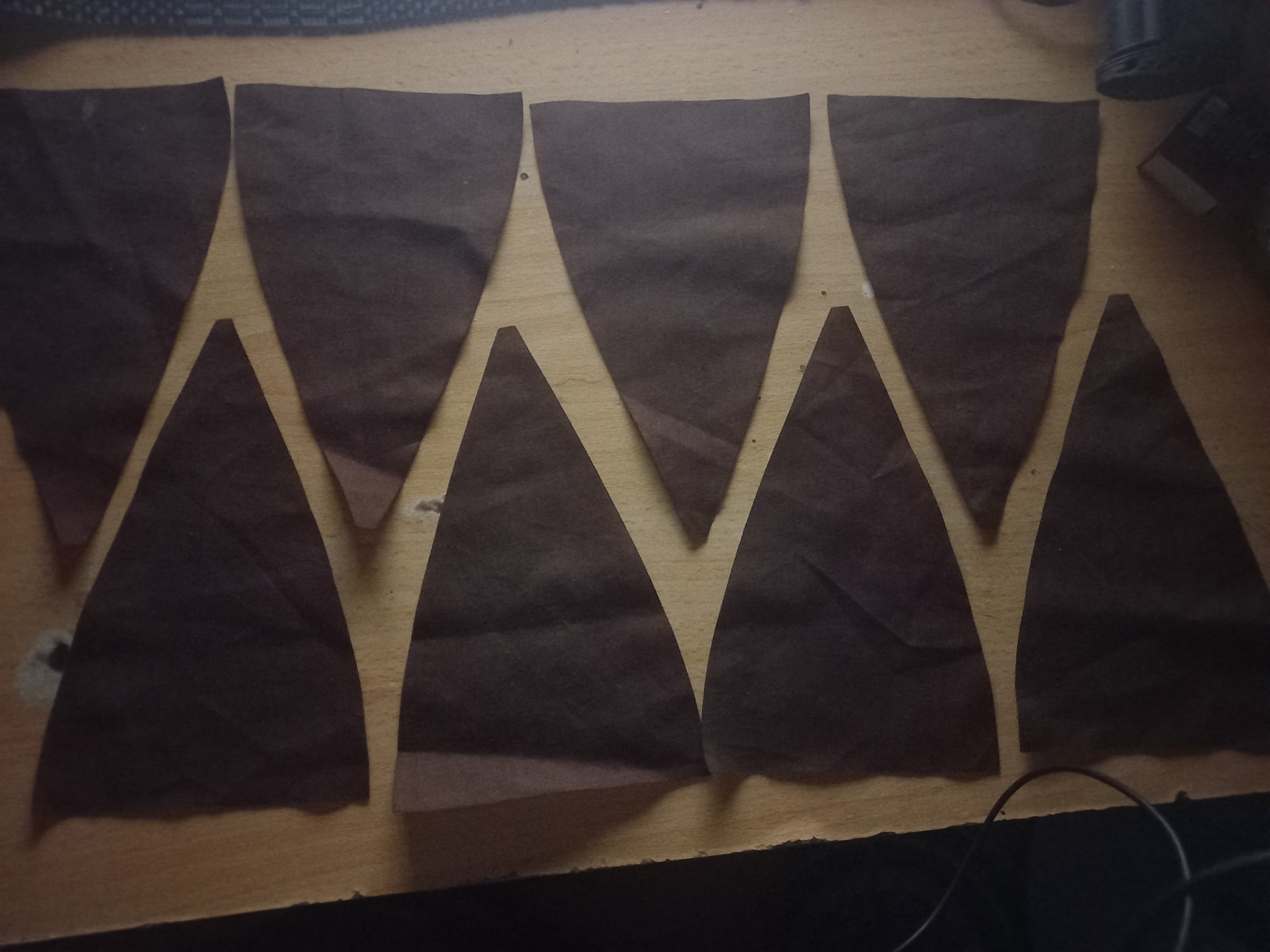
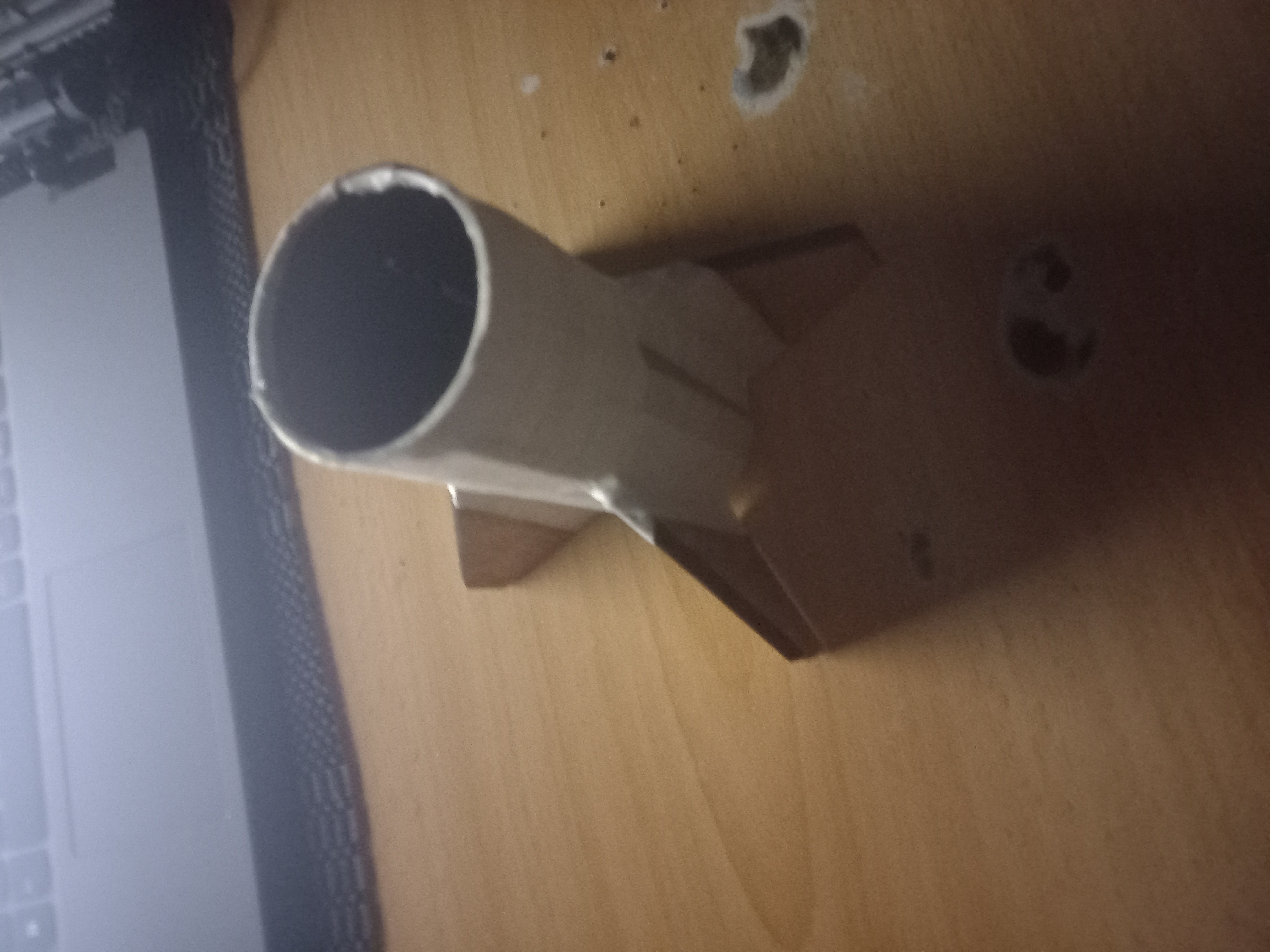
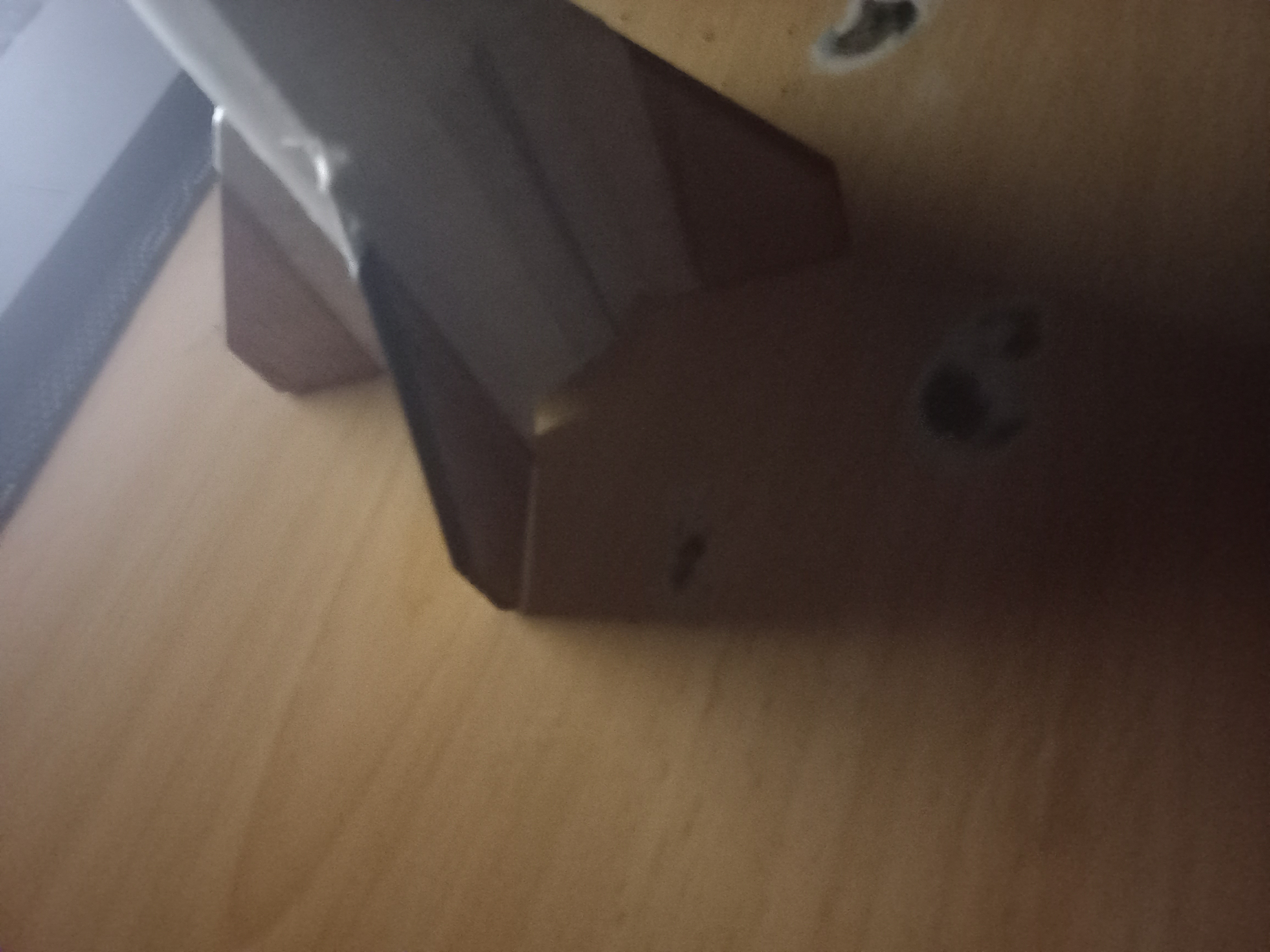
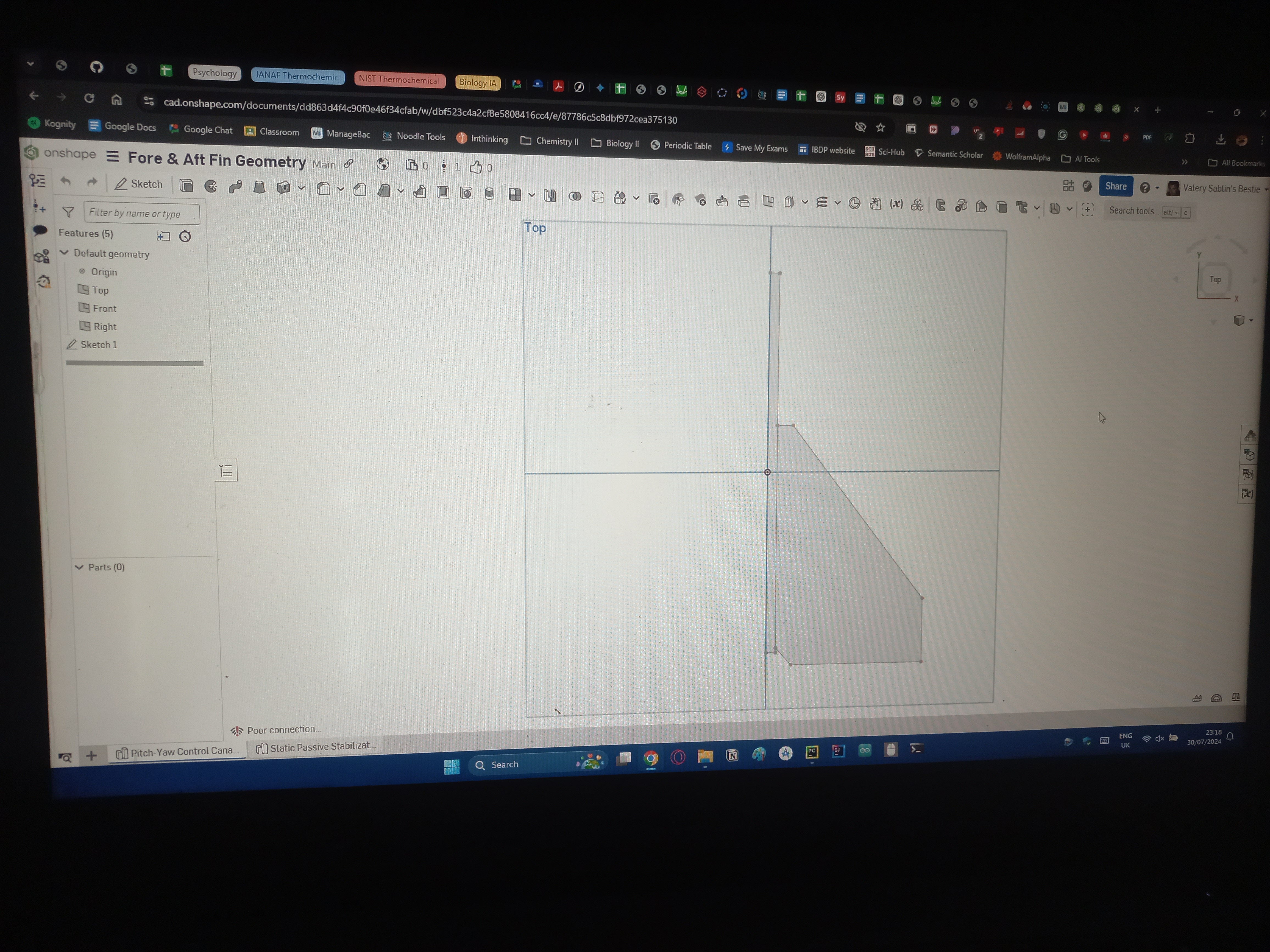
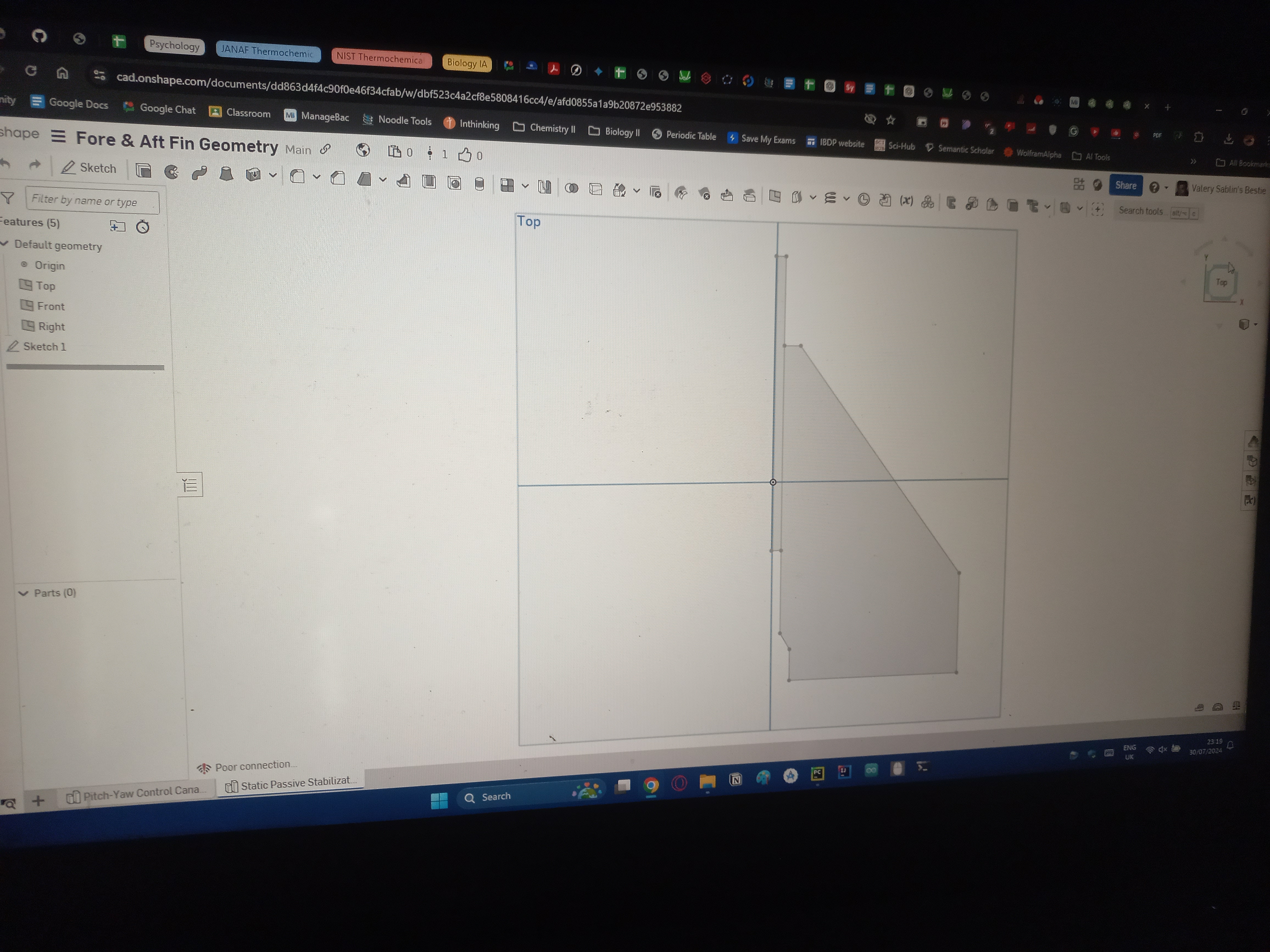
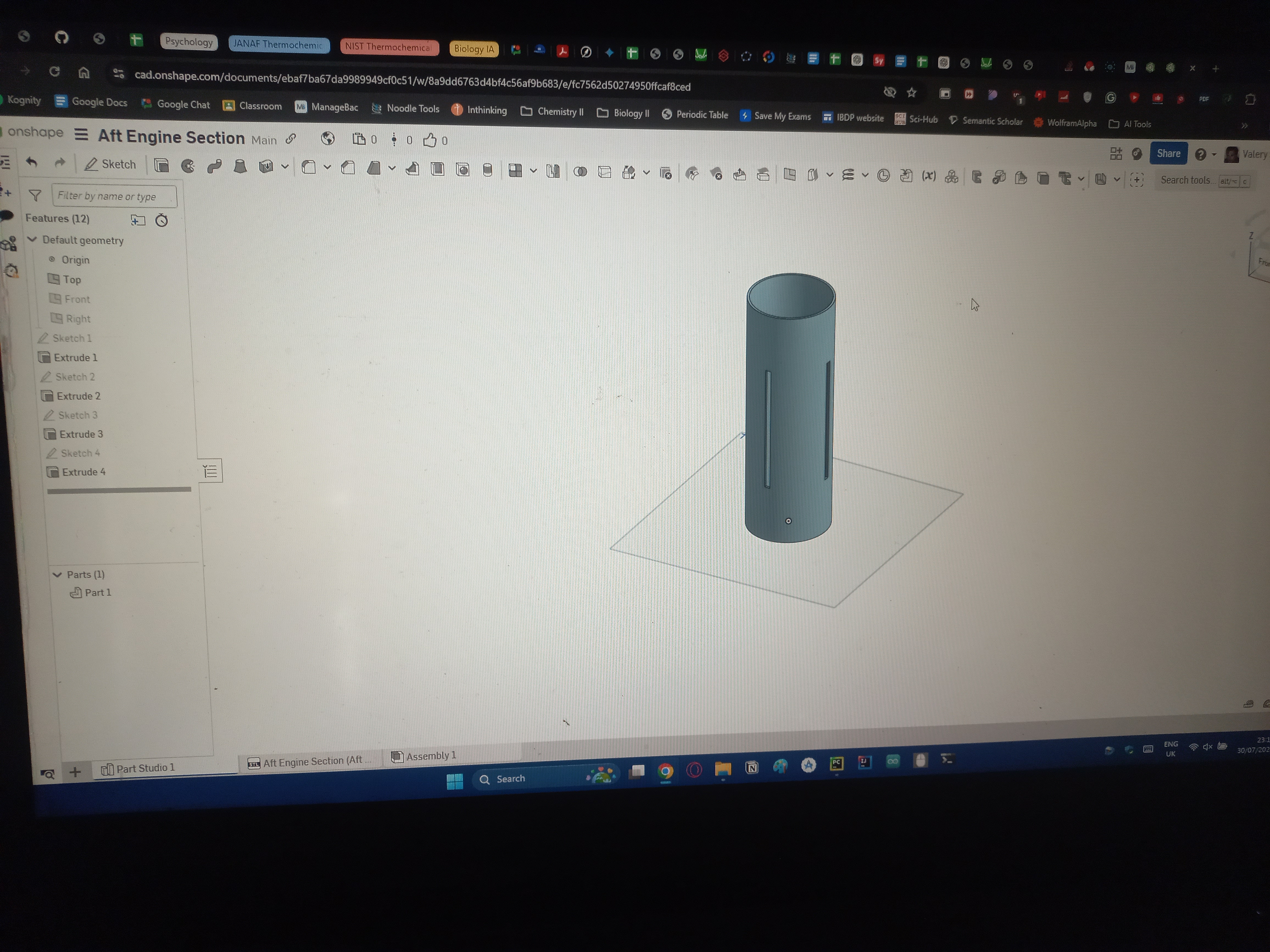
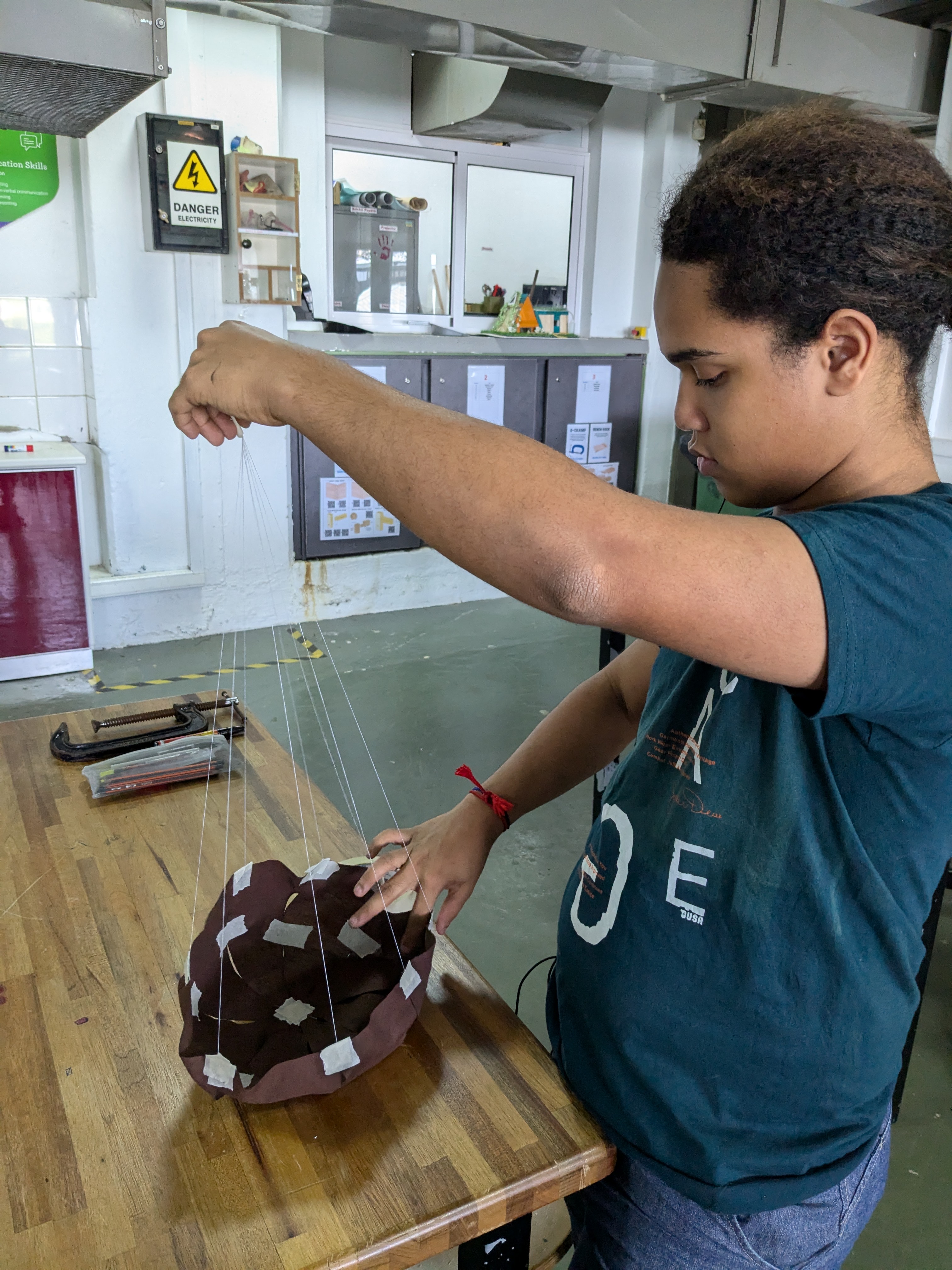
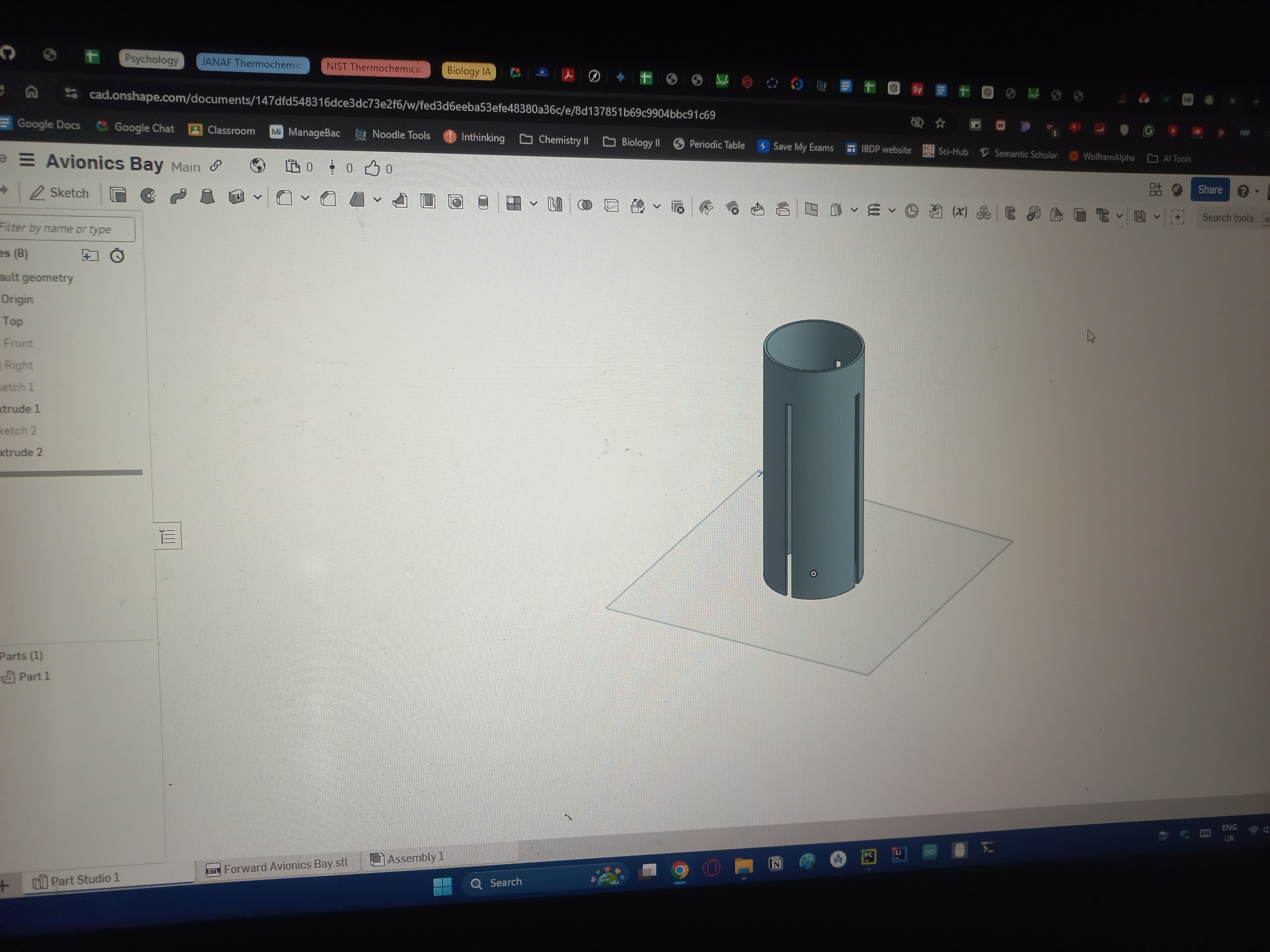
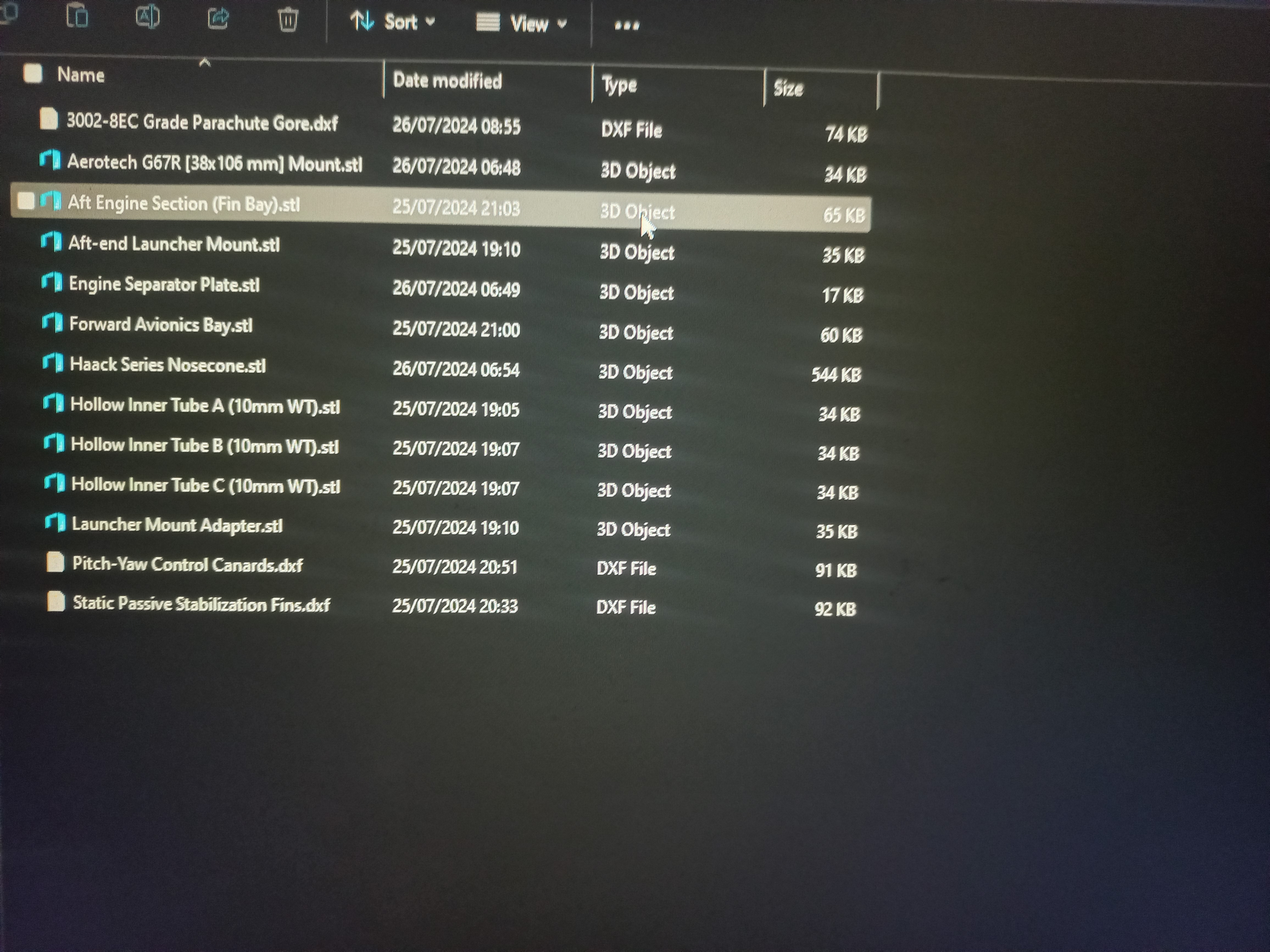
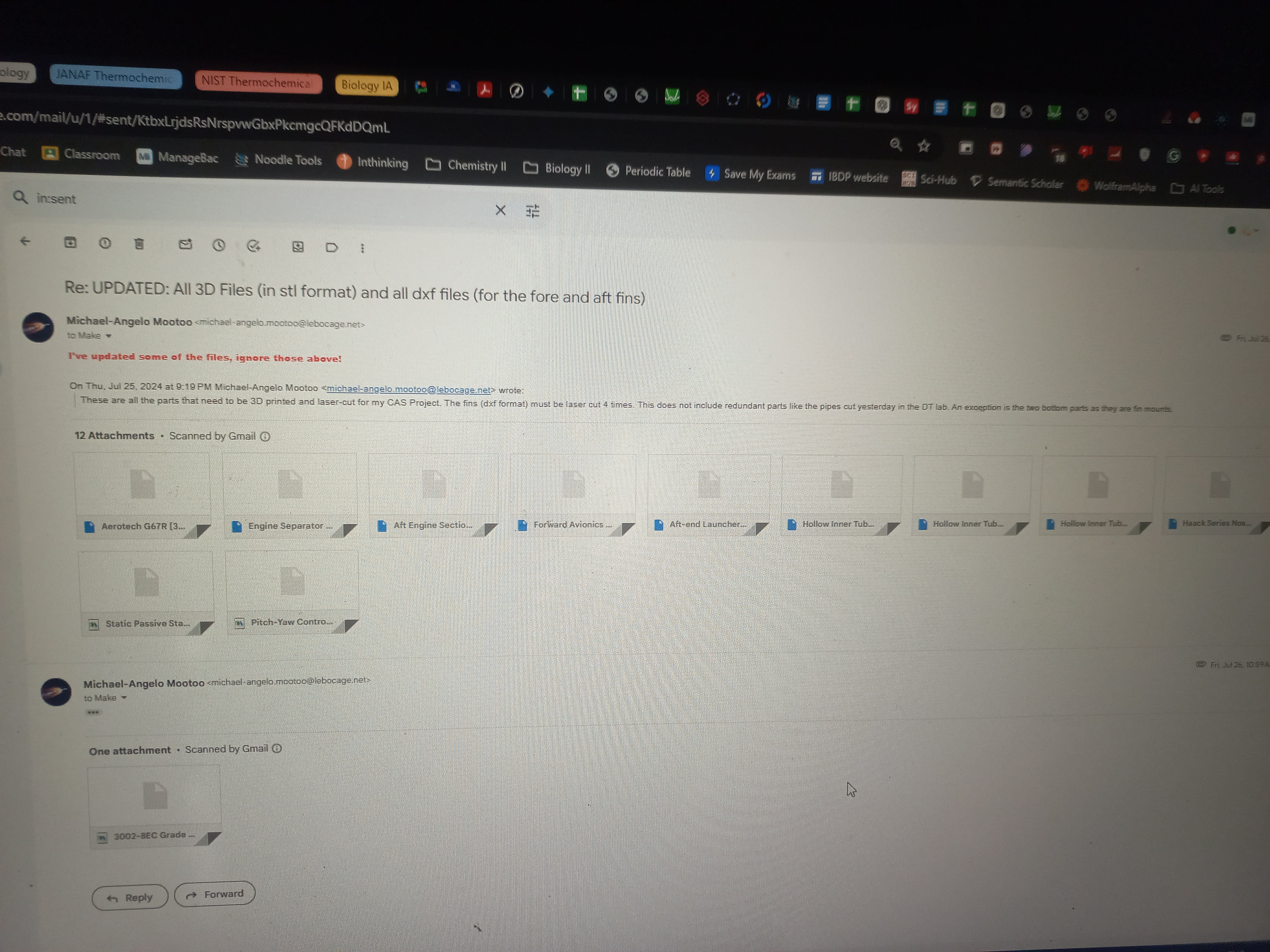
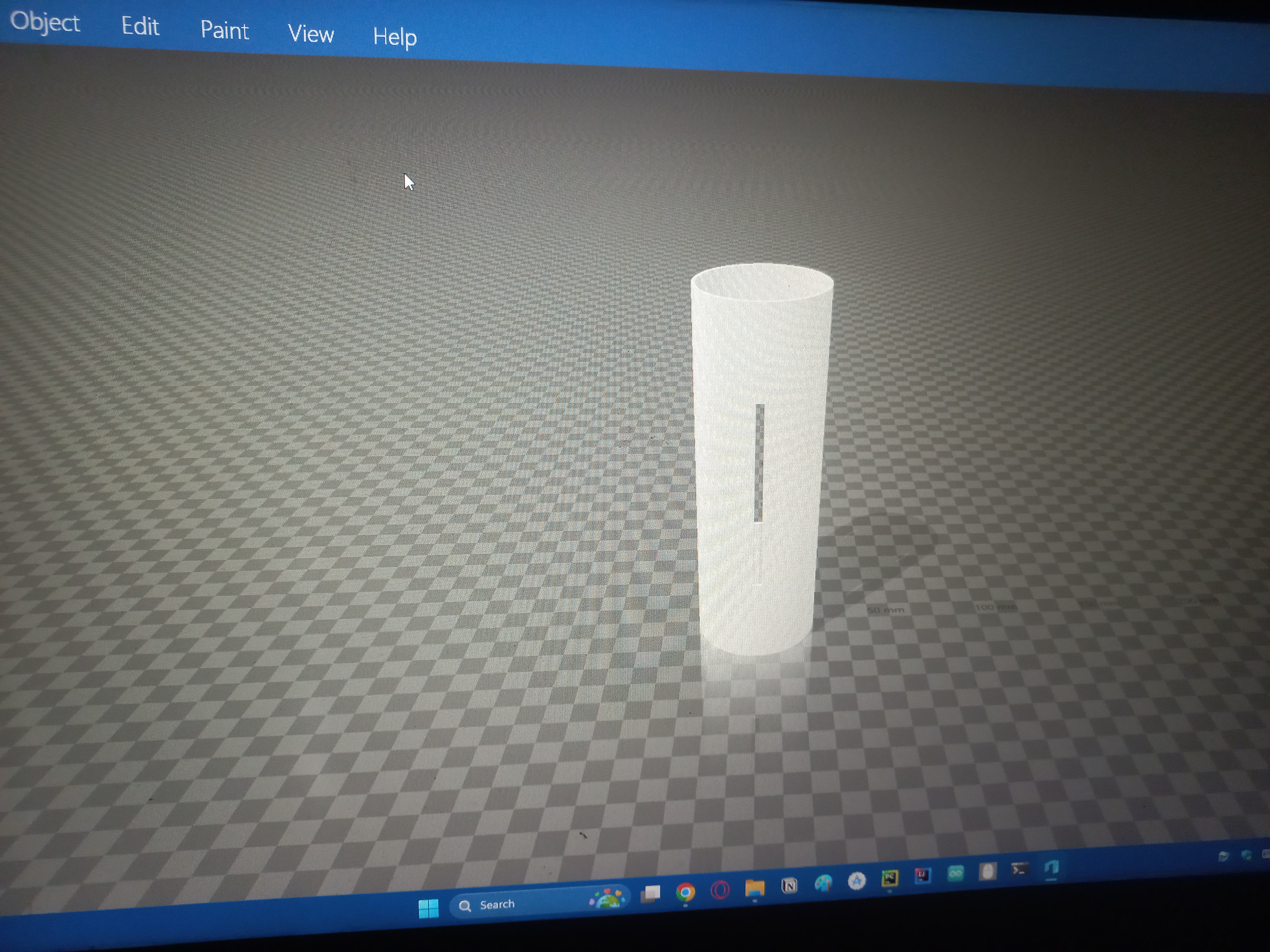
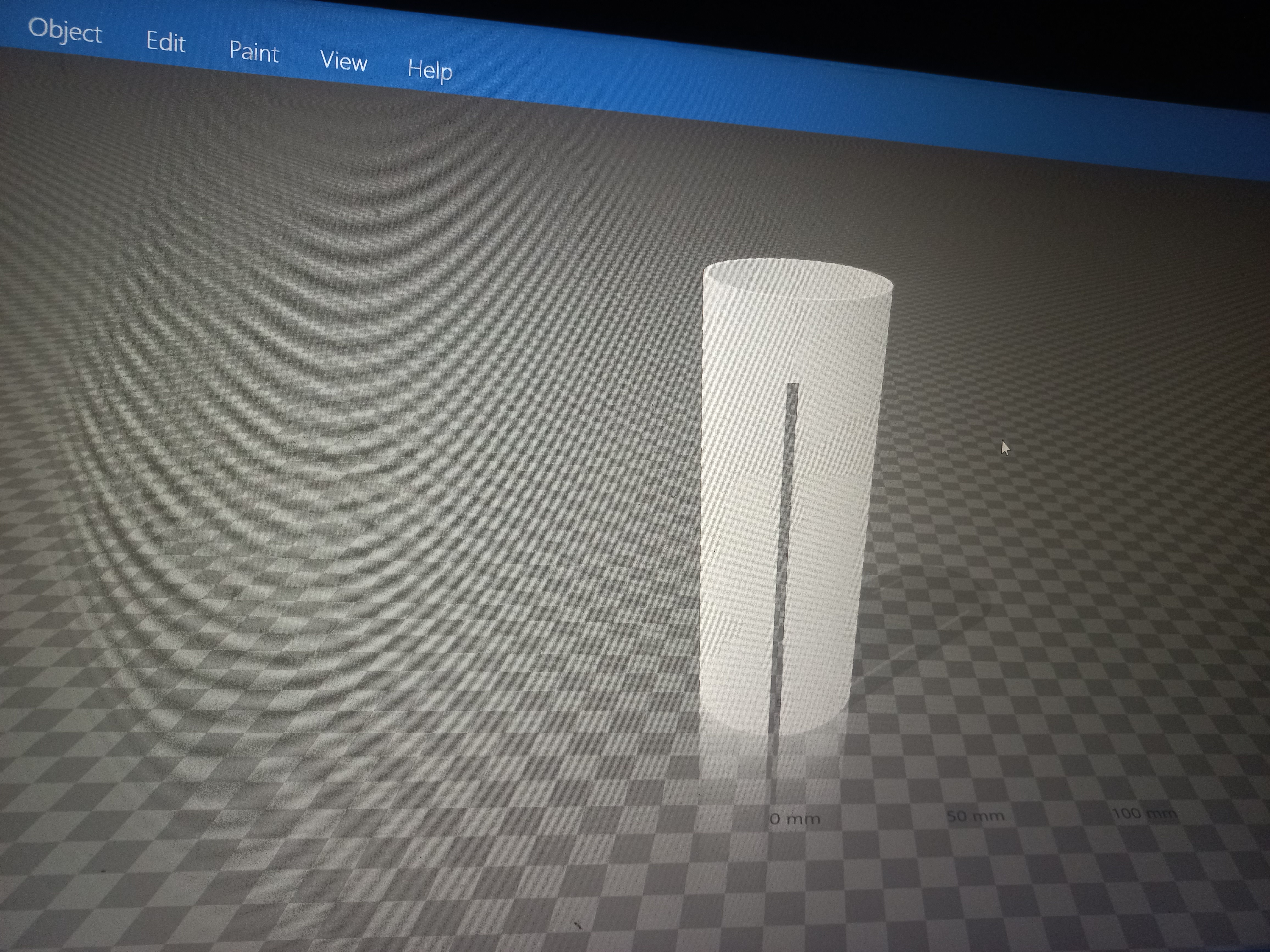
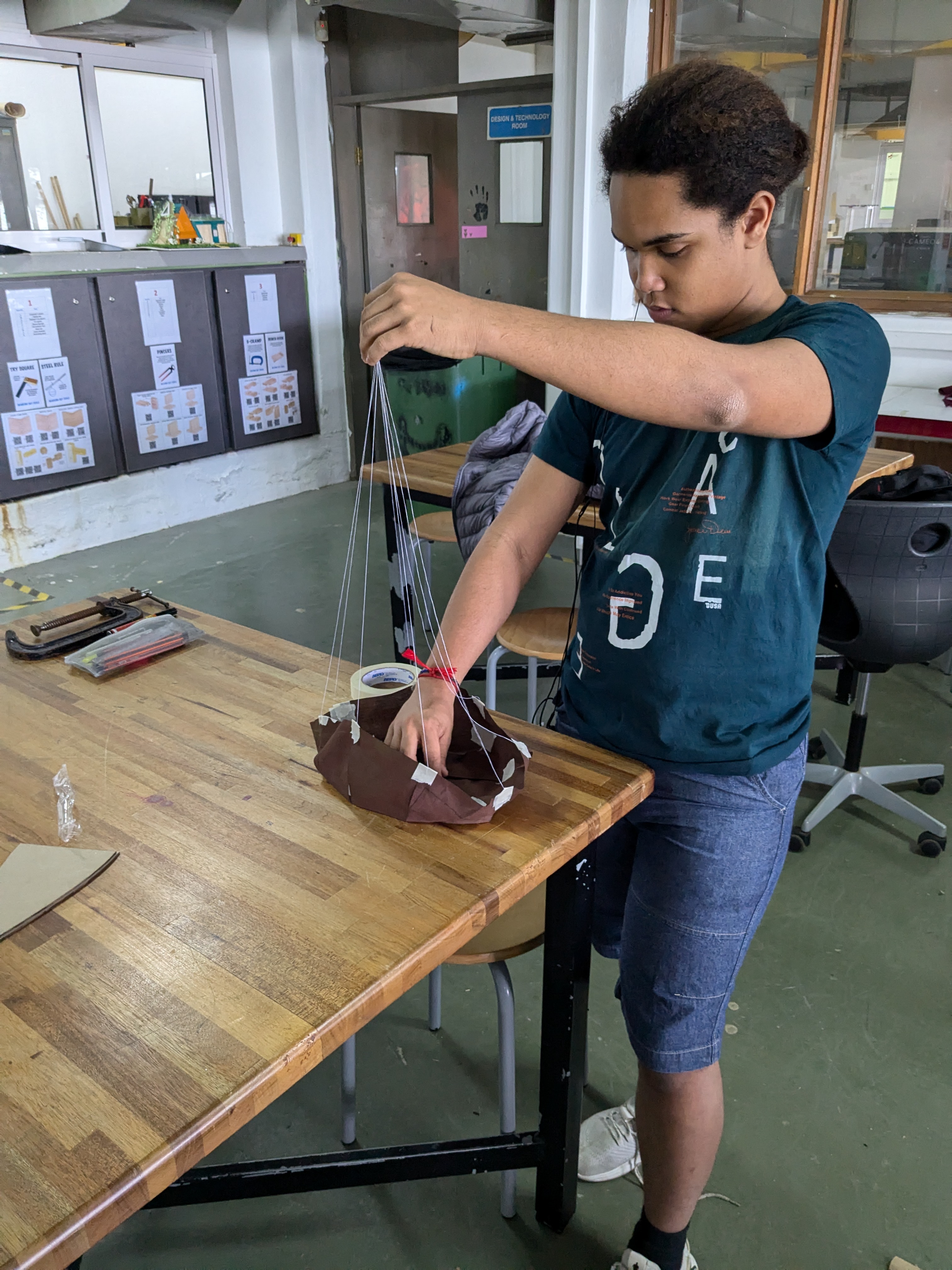
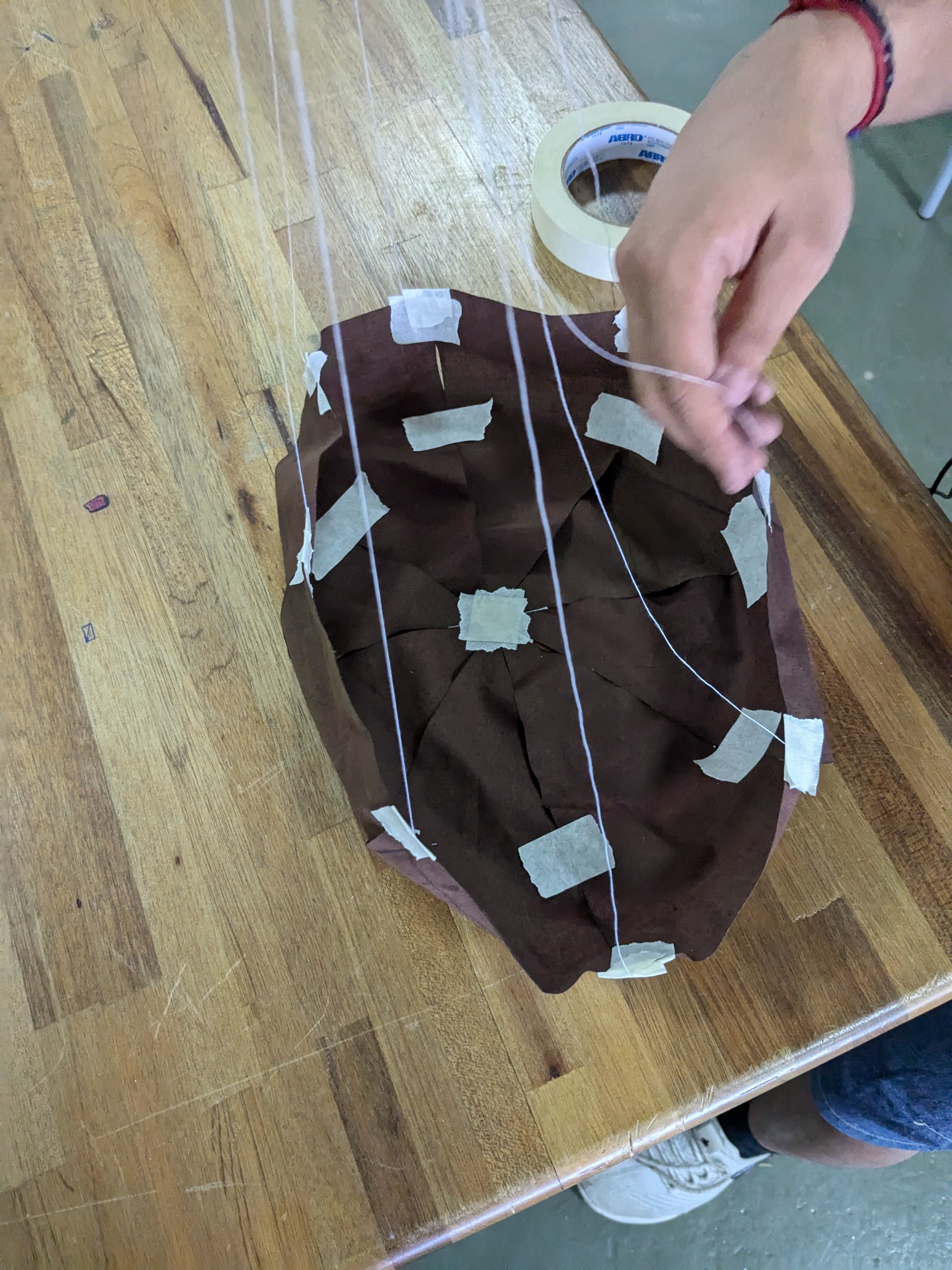
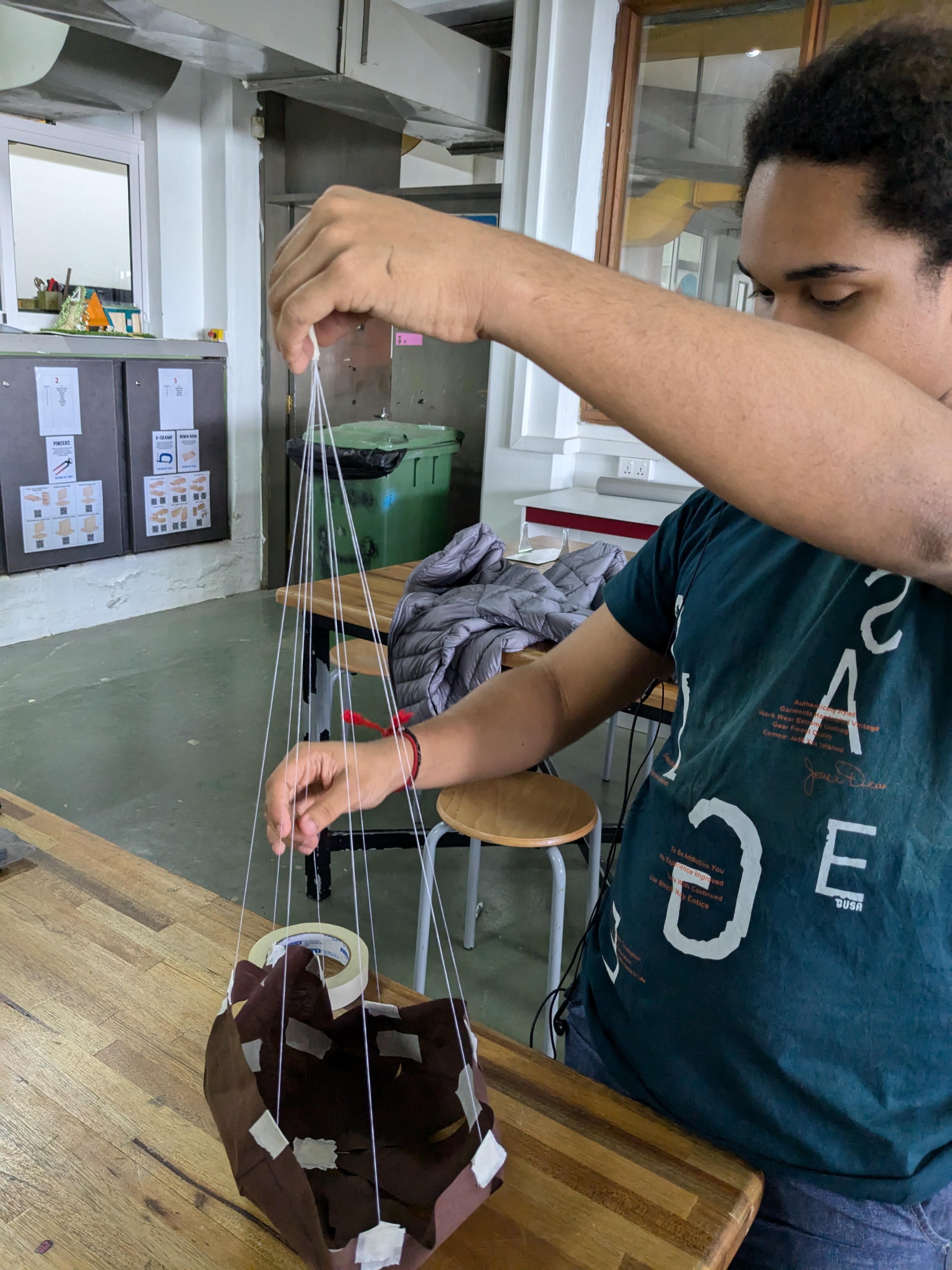